
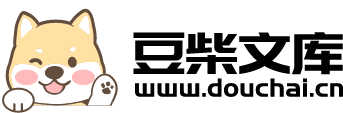
一种严格定义下切削加工的零件轮廓误差预测方法和系统.pdf
邻家****66
亲,该文档总共15页,到这已经超出免费预览范围,如果喜欢就直接下载吧~
相关资料
一种严格定义下切削加工的零件轮廓误差预测方法和系统.pdf
本发明公开了一种严格定义下切削加工的零件轮廓误差预测方法和系统,属于数控加工技术领域。首先给出轮廓误差的严格定义,避免了在大曲率零件计算过程中定义失效的问题;其次采用系统辨识的方法代替复杂的坐标变换,建立进给伺服系统模型;接下来采用局部搜索的方法确定目标插补点,同时采用局部直线插补的方式拟合加工轨迹,并且根据理论插补点与实际插补点的位置关系分别求解轮廓误差,提高了计算效率,适用于复杂零件轮廓误差的预测。本发明方法同时考虑了轮廓误差的预测效率与计算准确性,适用于大曲率零件轮廓误差的预测。
减小轮廓加工误差的方法和系统.pdf
本发明涉及一种减小轮廓加工误差的方法和系统。所述方法包括以下步骤:获取震荡周期,并根据所述震荡周期计算延迟时间值;预估系统特性,计算系统特性参数,并根据系统特性参数计算分配系数;根据计算得到的分配系数值和延迟时间值对每个伺服周期中的原始插补位置进行卷积,将每个伺服周期分解成在所述延迟时间输出的数个部分。上述减小轮廓加工误差的方法和系统,通过在伺服周期中将原始插补位置分解为多个部分在不同延迟时间输出,从而对原始规划路径进行了处理,改善系统响应,减小了轨迹的轮廓误差,提高了加工精度。
五轴机床加工零件轮廓误差预测方法.pptx
五轴机床加工零件轮廓误差预测方法目录添加目录项标题五轴机床加工零件轮廓误差预测方法概述五轴机床加工零件轮廓误差的定义预测方法的重要性预测方法的分类五轴机床加工零件轮廓误差的来源机床误差刀具误差工件误差加工参数设置误差五轴机床加工零件轮廓误差的测量与评估测量工具与设备测量方法与流程误差评估标准与指标基于机器学习的五轴机床加工零件轮廓误差预测方法机器学习算法的选择与原理数据采集与预处理特征工程与模型训练预测结果评估与优化基于统计学的五轴机床加工零件轮廓误差预测方法统计方法的选择与原理统计过程控制回归分析与预测
五轴机床加工零件轮廓误差预测方法.docx
五轴机床加工零件轮廓误差预测方法魏敏张绍兴肖斌段小勇摘要:我国经济发展离不开工业进步,而作为工业生产重要工具,五轴机床生产加工的零件轮廓如果产生较大误差,将会直接影响后续产品质量。所以,需要对五轴机床加工零件轮廓误差预测方法探讨,从而摸索降低轮廓误差有效方案。利用侦测意特利五轴联动数控机床的进给轴与待加工零件相关信息,构建误差预测方案,可以实现对生产零件外部轮廓预测误差,对于提升零部件生产质量具有重要意义。Abstract:China'seconomicdevelopmentiscloselygeared
一种曲面加工零件表面轮廓误差的近似评估方法.pdf
本发明属于数控加工中轮廓误差计算领域,并公开了一种曲面加工零件表面轮廓误差的近似评估方法。其包括下列步骤:(a)以插补周期为单位分别记录每个周期内的指令插补点和反馈刀位点,将所有相邻的指令插补点连接形成三角网格曲面;(b)计算反馈刀位点集合中每个反馈刀位点到三角网格曲面的最短距离;(c)从反馈刀位点集合中选取多个反馈刀位点,实际测量选中的反馈刀位点处的轮廓误差,计算标定系数,使得每个反馈刀位点的实际轮廓误差与该反馈刀位点标定后的最短距离相等,利用标定系数计算轮廓误差。通过本发明,实现对加工零件百分之百检测