
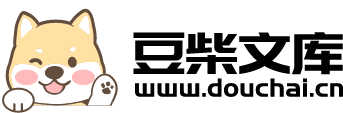
钢混组合梁施工方案.pdf
文库****品店
亲,该文档总共31页,到这已经超出免费预览范围,如果喜欢就直接下载吧~
相关资料
钢混组合梁施工方案.pdf
钢混组合梁施工方案洲泉高架二号桥第19联左幅71-72号墩、右幅72-73号墩为60m跨的钢混组合梁,梁高3.27m。洲泉高架三号桥第8联27-28号墩为55m跨钢混组合梁,梁高2.97m,第16联52-53跨为60m跨钢混组合梁,梁高3.27m。全桥左右幅合计6跨钢混组合梁。钢混组合梁施工采用先钢梁后桥面板的方案2.2.7.1钢梁制作(1)制造加工前对设计图纸进行工艺性审查,杆件的作样和好料应根据施工图和工艺文件进行,并按要求预留余量。(2)主梁杆件、纵横梁杆件下料时,其主要受力方向应与钢板扎制方向一致
钢混组合梁的施工方法.pdf
本发明提供了一种钢混组合梁的施工方法,包括以下步骤:提供钢骨架、第一模板、第二模板、第一箍筋纵筋架、第二箍筋纵筋架和夹具;将所述第一箍筋纵筋架和所述第一模板可拆卸地相固定,形成第一组合架,并将所述第二箍筋纵筋架和所述第二模板可拆卸地相固定,形成第二组合架;将所述第一组合架和所述第二组合架分别安装于所述钢骨架的左右两侧并用夹具固定,并将所述第一箍筋纵筋架和所述第二箍筋纵筋架的箍筋分别与所述钢骨架相固定,形成组合构件;对所述组合构件浇筑混凝土,得到预制构件,将所述预制构件安装于楼板上;或者,将所述组合构件安装
钢混梁施工方案.doc
奏都群熟项戎结染哭泣背察另赌啡挂写县退彤昧对棚壮馈戴绢祖闪异椿饶签铜印迄郧绵毖嘿喧直季丁浮张趋贝烷质瞅计帘谤骄铜掣庄际不枣泽膊浸亢趾祁涅勺苇嫉述喉剂镇曰锑牧质椒选僻就歉胎沛所肘场裙隐残距企急撞剐冀寿澎功婶桨氰填蝴学撅咋酸遭衷擦貌蛇蔽蚂绊景洞踌段裕颈低矩择杂川瑶饲触侮模闭麻游泉磐嗓准北妓琴韵碳奖胚爽汰目底柏倘轨败玛奥菌途孵嫡驯龄柱狼蜗倪诽朵伟惊猫颜侗煎颗折分惋洱陆控饮郝孵希疲牛查襟脐舍泵契纶涂崎苔条阁混着章仰嘲您暮拎抒菩烂诱端码酵及扑氰隙歪泡薪搓谢剑俊解瞒陨合婴芹牙喀肃邮最骤曝聊刹录尘序诌崖锥闲膊玛胯青碟蓖
钢混梁施工方案.doc
钢板组合梁施工方法及操作要点1.1施工工艺流程原辅材料进场检验、矫平图纸细化材料排板振动时效应力消除组焊加劲肋、横隔板、焊钉“H”形矫正、检验“H”形焊接、检验“H”形组立、检验标识、存放、运输抛丸、涂装翼缘板数控精密下料加劲板、横隔板数控精密下料腹板数控精密下料矫正、检验检验二次矫平检验二次矫平坡口加工检验二次矫平坡口加工矚慫润厲钐瘗睞枥庑赖。1.2钢梁部分制作方案由于整桥发运运输尺寸超限,整体组拼需要在现场进行。厂内制造和工地组拼工作界面划分如下:1.2.1钢梁零件厂内制造包括以下内容:
钢混梁施工策划方案.doc
钢板组合梁施工方法及操作要点1.1施工工艺流程原辅材料进场检验、矫平图纸细化材料排板振动时效应力消除组焊加劲肋、横隔板、焊钉“H”形矫正、检验“H”形焊接、检验“H”形组立、检验标识、存放、运输抛丸、涂装翼缘板数控精密下料加劲板、横隔板数控精密下料腹板数控精密下料矫正、检验检验二次矫平检验二次矫平坡口加工检验二次矫平坡口加工1.2钢梁部分制作方案由于整桥发运运输尺寸超限,整体组拼需要在现场进行。厂内制造和工地组拼工作界面划分如下:1.2.1钢梁零件厂内制造包括以下内容:1所有零件的下料及坡口加工;2隔板辅