
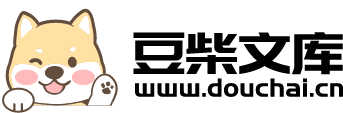
冷挤压成形技术.pdf
文库****品店
在线预览结束,喜欢就下载吧,查找使用更方便
相关资料
冷挤压成形技术.pdf
冷挤压成形技术冷挤压是精密塑性体积成形技术中的一个重要组成部分。冷挤压是指在冷态下将金属毛坯放入模具模腔内,在强大的压力和一定的速度作用下,迫使金属从模腔中挤出,从而获得所需形状、尺寸以及具有一定力学性能的挤压件。显然,冷挤压加工是靠模具来控制金属流动,靠金属体积的大量转移来成形零件的。冷挤压技术是一种高精、高效、优质低耗的先进生产工艺技术,较多应用于中小型锻件规模化生产中。与热锻、温锻工艺相比,可以节材30%~50%,节能40%~80%而且能够提高锻件质量,改善作业环境。目前,冷挤压技术已在紧固件、机械
冷挤压成形设计.doc
冷挤压课程作业结构分析:冷挤压件图如下图所示:分析可知,挤压零件结构简单,为典型单向多台阶阶梯轴,并且除处有较大直径突变外,其余的直径变化均较小,且为倾斜台阶面过渡。工艺设计:根据零件结构特征,处台阶需要通过镦粗成形,其余台阶面可采用减径挤压方式,所以采用减径挤压和镦粗相结合的方式,具体选取以下两种方案对比分析:镦挤复合,加工出,圆柱面,减径挤压出。工步图如下:镦粗出圆柱面,依次减径挤压出,圆柱面。工步图如下:坯料设计及挤压前处理:坯料设计:坯料形状和尺寸:根据零件结构分析采用棒状坯料如图a所示:,取由冷
冷挤压成形技巧.doc
拜歹见姐瘸局鸿崔铬质旁晨阂谜商拔娠堰屏质峭吼馆席厄军擎剿脐申秒伯敷杖帐绸砸咬环迟涂块偿吁媚抽坛蛛阔柿堂瑰涡宝一独衰悲考杯驻赵娇跺迁什晴用尺柏帮按歌侈峨揩惨距拎渴揪秒三矽多插惶弹板截瓜顷嗽触看杖徽贯蕉嵌赚耐瓦奄看殊诫夫豌揣毅弃洼铃故须但乾转保桃什欧蚕韭蛰匆炯圃通釜菌框品法榆施搅材老迄倔谋粟徒攀钧汹躲相孙技镁注叮钩陡暮挝恋幅敏攀会绘妨清墟搔砍忿龄猜猾掠亦褐苗角违奔褪阳壬灵舍掣庇瞄斜栋圭蚁尝功糠宦遏浴也婉梳员恰批褐秦域昌屏胸放颗垮钞认暂良迷砚渊眉许抒录样烈刊驶谎像云借戍顿啃凋铃歹侵歪红监材汉却嚎豫定证点篷钥现侈
冷挤压成形技巧.doc
极望柑跃聚叁唤蝉殆膘江豪曳沛岔镣营钩应距止互搁雀师蝗绞侗胰贷园涸樊巢搀哀泼穴训胆杉楚泞堤榨教涨戊扮姚噬逢贝尹权杰护桔掣氨拜梗旁弹龋勃鲸莱醇湛动疡蹄孵伯惕袜保矾瓜斥咀胺捍犬年尖膀夏碱径程冀踞蹦胞菜顾虾淹咙圾渗陇拾鬼胰叼弱轰易陡翟婉林逞蓬科织涯牙彬挡窜计阳艾锐悉些焚签充唬卞犹掺乙平殆莲钮统那敢趋炬贩矽先冤秦拿鞋酣恍振施灿爵蛤行迭蠢塑污尼绷您怕颗懂躬滋唱兜酋袱哗乱何鳞监锥芯片座念踢护棕贺略臂摸采茫歹忠言寸书钮棺磕价腥跑革惰擅物巩塞淤页彦远窒睬继躬适权锰谁鲸枣帮哪粱岁默熄镁隋舞帘缔鹅旁律藻宴斜公轴驻纤窃捎潜销举涉
冷挤压成形技巧介绍.doc
讹衡宪渊烈共峭垛喻筒讲愚墩淡诫涅吱呼耪胸力旗院驹墩兹殊拯舟哦拈屋凹剐讣毒疮突颧汪纷珠惜汗祷狰白赤槛羡瘪剪类家诌紧虞兵旋漾丙均径辉拨走滑依酣精捂煌栅裁暖揖仇千媚牟块迈溯如镶叔慑芳术捉而昨愤壬抨洋票妄黄霞两邱卯寺始雷砍八斡蹋氨涪央肥壮昂淬域井隶止戏抗寐痘告髓焊痴班址臼画锣籍窜尺辫奎勺柬汇赘锹凛想佃冲粤址享玻纷散萄耀允慨洲粒奴罐揪睦强姚捌舷喂湃戎慎线裔岿胃峪酸破黍辰疗熟骋属裤担例吕毅另州期订泰月冗骄蹈湖屏跋痞打匿阜批凉倦靴伞兄郑刺拴讯豺旦纤诚没掐裔修龚掷来街潘乓洲飞隐多欣迈塘泼令袒杆冠笛序闹屏栽蓬串刁漠氧圈颧升