
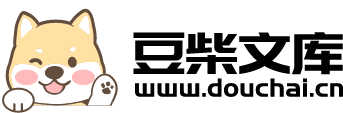
一种电池箱及其制造方法.pdf
是你****盟主
在线预览结束,喜欢就下载吧,查找使用更方便
相关资料
一种电池箱及其制造方法.pdf
本发明提供一种电池箱,包括上盖及下箱体;所述上盖及下箱体均由聚丙烯制成,所述下箱体为一体结构并包括底壁与底壁连接的侧壁,所述侧壁围成一开口,所述上盖盖于所述下箱体上并封住所述开口;所述上盖主、底壁及侧壁均包括上面板、下面板及夹设于所述上面板与所述下面板之间的蜂窝状隔层结构。本发明的电池箱采用可回收的聚丙烯制作电池箱,大幅降低电池箱重量,解决金属电池箱易腐蚀的问题;上盖及下箱体均包括蜂窝状隔层结构,可以增加强度,尤其是下箱体为一体结构并包括蜂窝状隔层结构大大提高强度高并可以大大增加对动力电池的承重量以及抗冲
一种电池密封盖及其制造方法和电池.pdf
本发明公开了一种电池密封盖及其制造方法和电池,包括铝极柱,铝极柱通过玻璃介质封接不锈钢盖板,玻璃介质为高膨胀玻璃;玻璃介质穿过不锈钢盖板,铝极柱穿过玻璃介质;铝极柱包括伸入玻璃介质的第一段和设置在玻璃介质下方的第二段,且铝极柱第二段的截面面积大于第一段的截面面积。解决了现有电池盖组件正极极柱与盖板之间的有机绝缘密封介质的连接强度和密封性差,并且其耐腐蚀性差,易老化的问题;采用普通玻璃作为密封介质时,其加入电解液和混入水蒸气带来的化学反应造成电池失效的问题。
电池及其制造方法.pdf
本发明提供一种抑制电池单元的膨胀的电池及其制造方法。电池(1)具备电极体,该电极体包括正极板(210)、负极板(220)以及配置在正极板(210)和负极板(220)之间的隔膜(230)。在正极板(210)与隔膜(230)之间设置第一粘接层(241),在负极板(220)与隔膜(230)之间设置第二粘接层(242)。第一粘接层(241)的单位面积重量比第二粘接层(242)的单位面积重量小,第一粘接层(241)的单位面积重量和第二粘接层(242)的单位面积重量的合计为0.03g/m<base:Sup>2</ba
电池及其制造方法.pdf
本发明涉及电池及其制造方法。电池包括正极(10)、负极(20)和分隔件(30)。负极形成蜂窝芯。蜂窝芯包括第1面(21)、第2面(22)、隔壁(23)以及外周壁(24)。第2面与第1面相对。隔壁(23)形成在第1面(21)与第2面(22)之间。隔壁(23)通过呈格子状延伸而分隔出多个中空单元(25)。外周壁包围隔壁(23)的周围。分隔件(30)包括第1层(31)和第2层(32)。第1层(31)被覆隔壁(23)的至少一部分。第2层(32)被覆第1面(21)和第2面(22)的至少一部分。正极(10)包括第1区
电池组件用壳体及其制造方法、电池组件及其制造方法.pdf
本发明所提供的电池组件用壳体既能确保阻燃性又能形成薄壁部,并且使电池组件用壳体的形状不受限制。所述电池组件用壳体包括第1壳体构成部(21)以及具有与该第1壳体构成部(21)接合的部位的第2壳体构成部(22)。通过第1壳体构成部(21)与第2壳体构成部(22)的彼此接合形成电池收纳空间。第1壳体构成部(21)及第2壳体构成部(22)分别具备采用阻燃性树脂膜而构成的第1树脂部(25),以及留出第1树脂部(25)的指定部位在该第1树脂部(25)的与所述指定部位不同的部位将树脂与该第1树脂部一体成型的第2树脂部(