
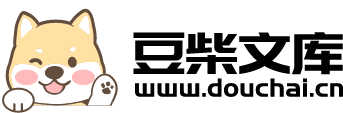
一种基于煤粉分布在线测量的风粉动态调平方法.pdf
音景****ka
在线预览结束,喜欢就下载吧,查找使用更方便
相关资料
一种基于煤粉分布在线测量的风粉动态调平方法.pdf
本发明公开了锅炉燃烧优化调节技术领域中的一种基于煤粉分布在线测量的风粉动态调平方法。本发明在传统磨煤机煤粉管道上安装了可调缩孔、煤粉流量在线监测系统、飞灰在线测量系统、煤粉分散器和煤粉控制阀;对一次风速、煤粉浓度和飞灰含碳量进行了调节。本发明依靠物理方式改变煤粉流动分配,并依据在线检测系统获得煤粉流动参数,通过可调缩孔和煤粉控制阀精细调整,实现了风、粉分配平衡,为锅炉燃烧优化技术的深入进行提供良好的前提条件。
煤粉管道风粉在线调平方法.pdf
本发明公开了一种煤粉管道风粉在线调平方法,监测煤粉浓度、煤粉流速两个参数,根据监测结果对一次风速和煤粉浓度的调平采取综合调节方案。调节顺序是先进行一次风速的渐进调平,在此基础上进行煤粉浓度调平。煤粉管道的风、粉在线调平是通过机组冷态和热态环境相结合进行的综合调平,弥补了单一冷态调平的较大偏差。一次风速的调节是通过可调缩孔实现的,在监测数据的基础上,缩孔由100%开度逐步渐缩调整,直到一次风速平衡为止;一次风速调平后,通过煤粉管平衡阀进行煤粉浓度的调平。本发明能有效地优化风、粉分布平衡性,配合二次风优化配置
一种电站锅炉煤粉电荷量在线动态测量的方法.pdf
本发明公开了一种电站锅炉煤粉电荷量在线动态测量的方法,包括以下步骤:步骤S1:电站锅炉的内部设置有煤粉管道,将需要进行煤粉电荷量在线动态测量的煤粉管道内安装一个测点,每个测点由一对传感器和一台信号处理单元构成,传感器与信号处理单元柜进行连接,信号处理单元通过现场总线与上位机连接;步骤S2:将传感器通过辅助安装结构固定安装在煤粉传输管道的内部,使得传感器的探头暴露在煤粉管道的内部,当煤粉管道中的介质流经过探头时;本发明,采用交流电荷感应技术测量,通过上下游传感器时产生的电荷信号的时差,测量精度不受介质成份的
一种基于机器学习的风粉在线测量方法.pdf
一种基于机器学习的风粉在线测量方法,通过试验获得样本数据,通过径向基神经网络算法对样本进行学习训练,得到模型参数;判断学习训练结果,然后通过在线模型导入并计算,得到实时测量值,即进行煤粉输粉管道速度及浓度的实时计算;判断实时测量结果:验证实时计算结果,如果符合要求则结束计算。本发明应用径向基神经网络算法建立数据模型,通过机器学习的计算拟合,得到煤粉输粉管道的风速、浓度等流动参数,为锅炉状态监测提供了可靠数据。
基于新型风粉在线监测的锅炉精细调平及优化技术.docx
基于新型风粉在线监测的锅炉精细调平及优化技术锅炉作为能源转换设备的核心部件,在工业生产和生活中起着非常重要的作用。然而,由于长期运行和烟气污染等原因,锅炉的运行效率和环境排放等问题已经成为亟待解决的难题。为了提高锅炉的运行效率和减少环境污染,锅炉精细调平及优化技术应运而生。随着科技的不断发展,新型风粉在线监测技术逐渐成熟,为锅炉的精细调平及优化提供了强有力的支持。新型风粉在线监测技术通过安装在锅炉燃烧系统中的传感器,实时监测锅炉的燃烧参数,包括风量、风温、风压、给煤量等,同时结合先进的数据分析和处理技术,