
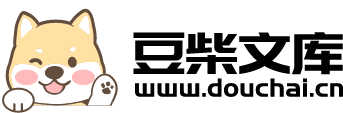
一种高强度、高模量沥青基纤维的制备方法.pdf
飞舟****文章
在线预览结束,喜欢就下载吧,查找使用更方便
相关资料
一种高强度、高模量沥青基纤维的制备方法.pdf
本发明公开了一种高强度、高模量沥青基纤维的制备方法,该制备方法按下述步骤进行:首先将高软化点沥青放入纺丝设备的喷丝料筒中,在氮气保护下升温至熔融纺丝温度,然后纺丝设备在320-340℃的高温条件下通过喷丝头挤出喷丝,得到生纤维;然后将生纤维置入预氧化炉内,通入热空气的同时对预氧化炉内的生纤维进行预碳化、碳化及再碳化等多阶段碳化,并冷却至常温即可得到高强度、高模量沥青基纤维。本发明的制备方法简单、产率高、反应过程温度低、可控性好,制备过程中产生的污染小、综合利用率高,制得的高强度、高模量沥青基纤维的抗张强度
一种高强度、高模量沥青基纤维用沥青的制备方法.pdf
本发明公开了一种高强度、高模量沥青基纤维用沥青的制备方法,该制备方法按下述步骤进行:首先将沥青与酚醛树脂按比例投入沥青调质釜内,然后升高炉温将原料熔化成液体,接着通入高温热空气使炉温继续缓慢升温至250-350℃后保持乳化热缩聚反应3-8小时;高温沥青通过高压输送泵输送至喷雾调质塔内的二流体喷嘴和高压空气混合后进行高压喷雾,沥青雾粉自由下落至喷雾调质塔的底部的过程中进行热缩聚反应;冷却后由喷雾调质塔塔底连续出料得高软化点沥青;将高软化点沥青、添加剂、固化剂混合后加入破碎机破碎,获得高强度、高模量沥青基纤维
一种高模量高导热沥青基炭纤维的制备方法.pdf
本发明公开了一种高模量高导热沥青基炭纤维的制备方法,首先通过常压氮气鼓泡吹扫的方法制备软化点在80~90℃的乙烯焦油沥青,然后向其中加入硼酸三乙酯,再通过加压热聚合及减压脱挥的方法制备含硼可纺中间相沥青;再经熔融纺丝、预氧化、碳化及石墨化制备高模量高导热沥青基炭纤维样品,其拉伸模量为800~900GPa、热导率为800~1000W/m·K。本发明将硼元素通过化学反应的方法引入到中间相纺丝沥青中,实现了硼元素均匀可控的添加,解决了常规方法硼元素添加不均的难题;硼元素在后续沥青基炭纤维的制备过程中有效的启到催
一种高模量高导热沥青基炭纤维连续长丝的制备方法.pdf
本发明公开了一种高模量高导热沥青基炭纤维连续长丝的制备方法,首先将初纺沥青纤维连续长丝束通过回丝机构退绕到氧化碳化网带炉上进行连续氧化碳化处理,在氧化过程中通过调节不同温区的氧浓度实现其分子结构的调控,待纤维获得一定强度后再重新进行卷绕;然后再通过开卷、高温碳化、石墨化、上浆、干燥及收卷等过程制得高模量高导热沥青基炭纤维连续长丝产品,其拉伸模量为900~950GPa、热导率为900~1100W/m·K、拉伸强度为2~3.5GPa、连续长度可达20000m以上。本发明在实现沥青纤维连续化制备的前提下,通过调
高强度高模量碳纤维的制备方法.pdf
高强度高模量碳纤维的制备方法,其特征在于,将聚丙烯腈共聚纤维置于温度为160~180℃的热处理炉中,热处理时间为4~8分钟,并施以2~12%的牵伸比,以聚丙烯腈共聚纤维中无定形区分子链的取向度fa值作为结构控制指标。选择fa值在35~45%范围的纤维进行热氧稳定化、低温碳化和高温碳化处理制得碳纤维。本发明制得的碳纤维的拉伸强度高于3.6GPa、拉伸模量高于240GPa。