
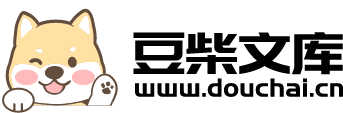
一种锰锌铁氧体料粉制备方法.pdf
Wi****m7
在线预览结束,喜欢就下载吧,查找使用更方便
相关资料
一种锰锌铁氧体料粉制备方法.pdf
本发明公开了一种锰锌铁氧体料粉制备方法,是以Fe2O3、Mn3O4、ZnO为主要原料,通过自动配料、高速分散、砂磨、压滤、双螺杆挤压造粒、预烘干、预烧、粗粉碎、细粉碎、喷雾造粒十个工序制成锰锌软磁铁氧体料粉。本发明的工艺解决了干法工艺预烧不均匀,湿法工艺成本较高的问题,同时,通过压滤可大幅度降低原材料中的Cl-等酸根离子,延长了回转窑炉管及排风管道的使用寿命周期,同时解决了废弃排放污染的问题,并且提高了产品的各项性能;具有较高的初始磁导率,同时具有良好的温度特性、频率特性、低的损耗、高的阻抗和良好的叠加性
湿法炼锌铁渣制备锰锌铁氧体粉料的研究.pptx
汇报人:CONTENTSPARTONEPARTTWO湿法炼锌工艺简介铁渣的来源与利用现状锰锌铁氧体的应用价值研究目的与意义PARTTHREE铁渣的化学组成分析铁渣的物相结构分析对铁渣进行预处理的必要性PARTFOUR实验原料与设备原料准备:湿法炼锌铁渣、锰盐、铁盐、氧化剂等混合:将原料混合均匀,形成混合物煅烧:将混合物进行煅烧,得到煅烧产物研磨:将煅烧产物进行研磨,得到细粉混合:将细粉与锰盐、铁盐、氧化剂等混合均匀,形成混合物煅烧:将混合物进行煅烧,得到煅烧产物研磨:将煅烧产物进行研磨,得到细粉混合:将细
湿法炼锌铁渣制备锰锌铁氧体粉料的研究.docx
湿法炼锌铁渣制备锰锌铁氧体粉料的研究摘要:本文以湿法炼锌铁渣为原材料,采用固相反应法制备锰锌铁氧体粉料。分别考察了反应温度、反应时间和浸泡时间对制备锰锌铁氧体粉料的影响,并通过扫描电镜(SEM)、X射线衍射(XRD)和振动样品磁强计(VSM)等手段对制备的样品进行表征和分析。结果表明,在反应温度为850℃,反应时间为4h,浸泡时间为2h的条件下,制备得到的锰锌铁氧体粉料有良好的磁性能、均一的颗粒形状和粒度分布,具有潜在应用于电子磁学领域的应用前景。关键词:湿法炼锌铁渣;锰锌铁氧体粉料;固相反应;磁性能;应
一种制备宽温低功耗锰锌铁氧体粉料的生产方法.pdf
本发明涉及锰锌铁氧体粉料生产技术领域,具体地说,涉及一种制备宽温低功耗锰锌铁氧体粉料的生产方法。包括以下步骤:获取电池极片;回收负极片;回收正极片;回收工业废渣;宽温低功耗锰锌铁氧体的生产;废液回收。本发明的优点在于:提高钴酸锂电池的回收率、降低铁氧体的生产成本、提高产品性能、带来可观的经济效益、节能减排,具有非常广泛的应用前景和经济价值。
一种锰锌功率铁氧体磁粉芯及其制备方法.pdf
本发明公开了一种锰锌铁氧体磁粉芯及其制备方法,其制备方法包括如下步骤:(1)配料:原料由主料和辅料组成,其中主料包括Fe2O3、ZnO、MnO或者Mn3O4,主料中各组分间的比例关系为53~55mol%的Fe2O3,32~34mol%的MnO、Mn3O4其中的一种或两者的混合,其余为ZnO;(2)冶炼:把Fe2O3、ZnO、MnO或Mn3O4按从下往上的顺序放入真空炉,然后盖上炉盖抽真空进行冶炼,冶炼温度1400~2000℃;(3)雾化制粉;(4)压制成型;(5)在真空退火炉中500~800℃退火1~2小