
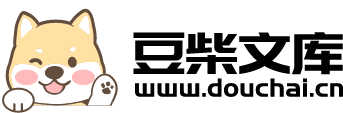
一种红土镍矿的煤基竖炉直接还原工艺.pdf
梦影****主a
在线预览结束,喜欢就下载吧,查找使用更方便
相关资料
一种红土镍矿的煤基竖炉直接还原工艺.pdf
本发明涉及一种红土镍矿的煤基竖炉直接还原工艺,所述红土镍矿的煤基竖炉直接还原工艺包括以下步骤:红土镍矿矿粉、煤粉、粘结剂和脱硫剂经过混匀、压块和烘干后与还原剂和脱硫剂混合,通过炉顶布料装置将混合料装入煤基竖炉的还原室中,混合料在煤基竖炉的还原室中经过预热段、还原段和冷却段,通过排料装置排出炉外,经过筛分、磨粉和磁选后,最终得到镍铁。本发明具有原燃料适应性广、产品质量好、规模化生产、作业率高、生产操作方便、能耗低、成本低、环保好等显著优点。
红土氧化镍矿转底炉煤基还原生产珠镍铁工艺.pdf
本发明公开了一种可降低生产成本的红土氧化镍矿转底炉煤基还原生产珠镍铁工艺,属于铁合金生产技术领域。该工艺包括如下步骤:a、将红土氧化镍矿原矿、还原煤及熔剂经细碎、配料、混合、造球后烘干制得干球;b、将干球送入转底炉进行还原,出炉后的高温熔块经水淬冷却、破碎、磁选,得到珠镍铁合金及炉渣。本发明采用转底炉作为还原设备,直接使用廉价、资源分布广泛的非焦煤为还原剂,采用煤气为主要能源,生产成本低,可在电力资源缺乏的矿山地区建厂应用,克服了传统工厂原料运输成本较高的制约条件,本发明工艺简单,易操作,易于投入规模化生
一种煤基竖炉直接还原工艺.pdf
本发明涉及一种生产海绵铁的煤基竖炉直接还原工艺,所述的生产海绵铁的煤基竖炉直接还原工艺包括以下步骤:铁精粉和粘结剂经过混匀、压块和烘干后与还原剂和脱硫剂混合,通过炉顶布料装置将混合料装入煤基竖炉的还原室中,混合料在煤基竖炉的还原室中经过预热段、还原段和冷却段后,通过排料装置排出炉外,然后通过热筛或冷筛后,可以直接装入熔炼装置,或者压块后再装入熔炼装置;上述筛下物经过磁选后全部回收利用。本发明具有工艺流程简单可靠、能够实现规模化生产、原燃料适应性强、能源利用充分、成本低、产品质量好、产品应用广、投资低等显著
竖罐式红土镍矿直接还原炉炉内热过程研究.docx
竖罐式红土镍矿直接还原炉炉内热过程研究竖罐式红土镍矿直接还原炉是一种常用于镍矿冶炼工艺的设备。在这个炉内,镍矿经过还原反应转化为金属镍,然后通过炉外收集和处理。本论文将对竖罐式红土镍矿直接还原炉内的热过程进行研究。第一部分:引言引言部分介绍竖罐式红土镍矿直接还原炉的背景和重要性,以及研究目的和论文结构。第二部分:竖罐式红土镍矿直接还原炉的工作原理本部分详细介绍竖罐式红土镍矿直接还原炉的结构和工作原理。包括炉体结构、内部反应过程、传热方式等内容。同时还可将炉内热过程与化学反应联系起来,分析热过程对还原反应的
日处理500吨红土镍矿竖炉直接还原海绵铁工艺方案.doc
日处理500吨红土镍矿竖炉直接还原海绵铁工艺方案红土镍矿情况说明:氧化镍矿基本上分为两类:一类是红土镍矿,另一类是硅酸镍矿,矿床的上部,由风化淋滤作用的结果,铁多,硅少,镁少,镍较低;矿床的下部,由于风化富集,镍多,硅多,镁多,低铁。镍较高,称之为镁质硅酸镍矿。成矿特点:红土镍矿通常分三个层次成矿:第一层:LateritieNickelore(红土镍矿)Ni:0.9~1.1%Fe:45~50%第二层:LimoniticNickelore(镍褐铁矿)Ni:1.4~1.9%Fe:20~30%第三层:Sapro