
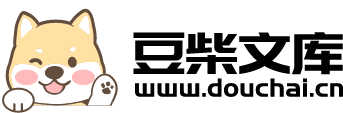
一种弥补转炉钢渣活性的方法.pdf
含秀****66
在线预览结束,喜欢就下载吧,查找使用更方便
相关资料
一种弥补转炉钢渣活性的方法.pdf
本发明转炉炼钢技术领域,具体涉及一种弥补转炉钢渣硅铝成分活性的方法。本发明所要解决的技术问题是提供弥补转炉钢渣活性的方法,包括以下步骤:a、将二氧化硅、三氧化二铝按重量比3︰1~2混匀并在900~1100℃进行烧结;烧结结束后冷却至室温,然后破碎,备用;b、将转炉钢渣进行破碎、筛分、磁选后,得粉料;c、将步骤a备用的烧结料与步骤b的粉料混匀后粉磨至要求粒度即可;其中,所述烧结料为粉料重量的10~30%。本发明方法以转炉钢渣为主,通过适当的添加硅铝成分,以弥补转炉钢渣中缺少的硅铝成分,从而达到转炉钢渣水化所
一种提高转炉钢渣活性的方法.pdf
本发明转炉炼钢技术领域,具体涉及一种提高转炉钢渣活性的方法。本发明所解决的技术问题是提高转炉钢渣活性的方法,包括以下步骤:a、将转炉钢渣破碎、筛分、磁选,得粉料;b、加水进行水化;c、水化结束后,控制含水量<3%,然后粉磨至要求粒度即可。本发明方法以转炉钢渣为主,通过适当的水化作用,对钢渣中的游离氧化钙进行适度消化,从而增加氧化钙在后期转变为氢氧化钙的数量,以提升钢渣在水泥或是混凝土中的胶凝性能,作为较佳的掺合料。
一种低活性转炉热泼钢渣胶凝活性激发剂及其制备方法.pdf
本发明提供一种低活性转炉热泼钢渣胶凝活性激发剂及其制备方法。所述低活性转炉热泼钢渣胶凝活性激发剂包括以下组分:复合醇胺、有机醇胺盐酸盐、氨基羧酸盐、无机电解质、多元醇和水。本发明的低活性转炉热泼钢渣胶凝活性激发剂原料组分安全环保,制备方法简便,掺加量低,性能稳定且适应性好,可显著提升低活性转炉热泼钢渣的胶凝活性,极大促进低活性转炉热泼钢渣在水泥和混凝土中的应用,助力实现钢渣整体的“零排放”。
一种添加硅酸三钙来提高转炉钢渣活性的方法.pdf
本发明公开的是金属冶炼技术领域的一种添加硅酸三钙来提高转炉钢渣活性的方法,包括以下步骤:a、对转炉钢渣进行破碎、筛分、磁选后获得0~15mm的粉料;b、往得到的转炉钢渣粉料中添加硅酸三钙成品,加入量为转炉钢渣质量的10~30%;c、将步骤b得到的粉料进行混匀、研磨后用于水泥或是混凝土掺合料。本发明的有益效果是:通过直接将硅酸三钙成品添加到转炉钢渣中,在一定程度上起到了弥补转炉钢渣中硅酸三钙成分和相应水化所需的作用,大大提高了转炉钢渣的活性,使其可用作水泥或混凝土掺合料,从而使转炉钢渣得到更广泛的应用。
一种转炉钢渣处理分离方法.pdf
一种转炉钢渣处理分离方法,包括氧化、热泼、筛分、酸浸、分离、沉淀、粉碎等步骤,有效地分离了转炉钢渣中的各个物质,成功的实现了炉渣的循环利用,且低成本的提取了磷酸盐产品,最大程度的发挥了转炉钢渣的价值,可根据不同粒级的钢渣的含铁性质,设置不同种类不同磁场强度的筛选设备,将钢渣中的铁全部回收,产生的尾渣也能进行进一步加工,实现钢渣的完全利用,最大程度的发挥了转炉钢渣的价值,本发明提供的一种转炉钢渣处理分离方法,具有工艺简单、设备要求低、生产效率高、成本低的优点,具有良好的市场推广前景。