
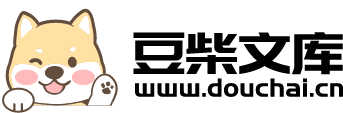
一种防开裂多孔砖及其制备方法.pdf
努力****爱静
在线预览结束,喜欢就下载吧,查找使用更方便
相关资料
一种防开裂多孔砖及其制备方法.pdf
本发明涉及房屋承重砖的技术领域,特别是涉及一种防开裂多孔砖及其制备方法,其可以对废弃资源进行回收利用,减少资源的浪费,并且可以提高多孔砖质量,减少开裂,延长使用寿命;包括以下百分比的原料:赤泥30%‑40%、煤矸石25%‑35%、炉渣15%‑20%、粘土12%‑18%和粘合剂1%‑3%;其制备方法包括以下步骤:(1)破碎研磨;(2)筛分除杂;(3)物料混合;(4)陈化处理:将混合后的物料导入陈化仓内进行3‑5天的陈化处理;(5)挤压成型:将陈化后的物料再次使用搅拌机进行搅拌后,通过挤压成型机挤出成型,得到
一种防开裂多孔砖及其制备方法.pdf
本发明提供了一种防开裂多孔砖及其制备方法,采用如下原料制备:尾矿泥200‑500重量份、粉煤灰40‑80重量份、深基坑土干粉50‑100重量份、高氯酸钾1‑5重量份、蒙脱土10‑30重量份、植物秸秆粉20‑40重量份,电炉钢渣粉15‑30重量份、生石灰4‑10重量份。与现有技术相比,本发明以尾矿泥、粉煤灰、深基坑土干粉、高氯酸钾、蒙脱土、植物秸秆粉,电炉钢渣粉、生石灰为原料,各个原料相互作用、相互影响,提高了制备的多孔砖的防开裂性能,强度较高。
一种防开裂白底漆及其制备方法.pdf
本发明公开了一种防开裂白底漆,其特征在于,按质量份数计,包括如下原料:PE树脂40‑60份、钛白粉5‑10份、PE防绿化剂0.1‑0.5份、消泡剂0.1‑0.5份、气相二氧化硅0.1‑0.5份、PE膨润土浆1‑5份、滑石粉20‑30份、透明粉5‑15份、硬脂酸锌1‑5份、流平剂0.1‑0.5份、甲苯3‑6份。本发明制备的产品漆膜防开裂性能佳,干燥后漆膜残留气味极低,填充性好,附着力好,打磨性优。产品在低温环境下有优异的干燥速度,打磨不粘砂纸,在高温环境下涂装不会产生针孔、白点等不良现象。
一种防开裂耐腐蚀砂浆及其制备方法.pdf
本发明公开了一种防开裂耐腐蚀砂浆及其制备方法,具体涉及建筑施工砂浆技术领域,包括:水泥、乳胶粉、玄武岩纤维、水、石英砂和复合增强剂。本发明可有效提高防开裂耐腐蚀砂浆的耐磨性能、耐腐蚀性能、耐高寒性能,可有效防止砂浆产品在高寒高原环境下的防开裂和防腐蚀性能;可制成纳米银颗粒、石墨烯和氧化石墨烯的复合材料;可对纳米二氧化钛进行改性处理,然后将改性后的纳米二氧化钛与氧化石墨烯进行复合;聚酰亚胺纤维为复合增强剂中的支撑网络,中空玻璃微珠可作为支撑框架,可有效加强复合增强剂的稳定性和安全性,进而保证砂浆的耐磨性能、
一种防开裂磁性材料及其制备方法.pdf
本发明公开了一种防开裂磁性材料及其制备方法,其中,该防开裂磁性材料的主料包括Fe2O350-54mol%,ZnO8-12mol%与MnO余量。该防开裂磁性材料的制备方法包括:按主料配比,湿法制粉,并采用平衡控温烧结工艺,在回转预烧窑炉中进行预烧处理;在二次砂磨工序,添加辅料,砂磨120min后,将含有辅料的预烧料料浆打入料浆池搅拌;在二次砂磨工序到二次喷雾造粒工序,将生料进行二次砂磨120min,按生料和正常料浆配比,再将生料料浆打入同一料浆池,加入1%的PVA,搅拌均匀后,进行二次喷雾造粒处理。本发明所