
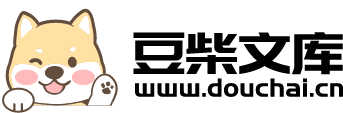
一种原位气相沉积法烧制仿钧红釉的方法.pdf
元容****少女
亲,该文档总共13页,到这已经超出免费预览范围,如果喜欢就直接下载吧~
相关资料
一种原位气相沉积法烧制仿钧红釉的方法.pdf
本发明公开了一种原位气相沉积法烧制仿钧红釉的方法,具体是将长石、石英、滑石、方解石及纳米氧化铝制成的釉浆涂敷在陶瓷素坯表面,得到施釉陶瓷素坯,将施釉素坯干燥后与石墨基复合材料一起置于马弗炉中烧制,最后得到具有仿钧红釉呈色效果的钧瓷产品。本发明将含铜的石墨基复合材料与施釉陶瓷素坯一起置于马弗炉中,在空气气氛条件下,利用烧制过程中石墨的不充分燃烧产生还原性一氧化碳,同时还利用烧制过程中产生的铜蒸汽,通过原位气相沉积法制备得到釉质莹润的仿钧红釉,解决了传统钧红釉需要在釉料中添加铜元素化合物及需要还原性气氛的问题
一种广钧红釉及其烧制方法.pdf
一种广钧红釉及其烧制方法,原料包括混合料和占混合料总质量0.01~0.55%的甲基纤维素及0.2~1.1%的三聚磷酸钠,所述混合料由以下质量百分比的陶瓷厂常用原料组成:30~50%长石、15~30%石英、5~20%石灰石、8~20%烧滑石、3.0~25%高岭石矿类粘土、0~2.00%牛羊骨灰、0.1~0.50%SnO、1~5%CuO和1‑5%SiC,其中SiC/CuO质量比为1~1.8。三段台阶保温烧成广钧釉制度方法成本低廉、不需对设备进行更新改造。配制的广钧红釉配方原料易得,制备工艺简单,釉面光滑平整,
钧红釉探索与烧制工艺.docx
钧红釉探索与烧制工艺钧瓷是我国宋代五大名窑之一,产于中国河南禹州市,是世界上最早的铜红釉瓷的发源地,堪称一切窑变之祖。河南禹州市神后镇是钧瓷的发源地和故乡,古代窑址遍及神后镇布周边,在禹州市境内有168处之多,尤以神后为中心,形成一个庞大的“钧窑”系延续千余年。有诗赞曰“钧瓷始于唐,宋代盛名扬,光辉照寰宇,神后是故乡”。多年来,对于钧瓷的历史、艺术、窑变艺术等的起源众说不一。对钧瓷窑变釉系也众说不一,那么现在我根据史料,考古发现的各时期瓷片,对钧瓷的烧制、工艺及各烧成阶段的问题进行一些探讨和大家交流,以求
钧红釉探索与烧制工艺.docx
钧红釉探索与烧制工艺钧瓷是我国宋代五大名窑之一,产于中国河南禹州市,是世界上最早的铜红釉瓷的发源地,堪称一切窑变之祖。河南禹州市神后镇是钧瓷的发源地和故乡,古代窑址遍及神后镇布周边,在禹州市境内有168处之多,尤以神后为中心,形成一个庞大的“钧窑”系延续千余年。有诗赞曰“钧瓷始于唐,宋代盛名扬,光辉照寰宇,神后是故乡”。多年来,对于钧瓷的历史、艺术、窑变艺术等的起源众说不一。对钧瓷窑变釉系也众说不一,那么现在我根据史料,考古发现的各时期瓷片,对钧瓷的烧制、工艺及各烧成阶段的问题进行一些探讨和大家交流,以求
一种复合钧花釉的釉料及钧花釉钧瓷的烧制工艺.pdf
本发明公开了一种复合钧花釉的釉料及钧花釉钧瓷的烧制工艺,它是将黑药、赤铁矿、黄长石、本药、石英石、方解石、铜矿石、氧化铜等原料通过湿法球磨工艺加工,分别制成底釉和面釉,再通过沾釉法均匀施于胎体的表面,最后放入炉窑内烧制成钧花釉钧瓷。该工艺烧成制度简单易控,组成配方简单,施釉工艺便捷,成品艺术效果突出。