
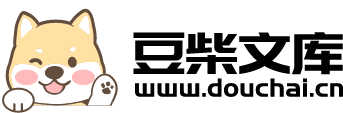
一种低热值铁水转炉冶炼方法.pdf
映雁****魔王
在线预览结束,喜欢就下载吧,查找使用更方便
相关资料
一种低热值铁水转炉冶炼方法.pdf
本发明公开了一种低热值铁水转炉冶炼方法,所述冶炼方法采用转炉单渣留渣法,包括以下工序:1)留渣工序;2)装入工序;3)吹炼工序;后期使用副枪测量TSC,根据TSC测量数据和终点目标计算供氧量和冷料加入量吹炼至终点提枪;使用副枪TSO测量钢水终点数据。本发明的主要目的是在不影响废钢比的情况下解决低热值铁水转炉冶炼过程化渣困难,粘枪、粘烟罩、脱磷率低等问题。
一种低硅铁水的转炉冶炼方法.pdf
本发明提供一种低硅铁水冶炼的方法,采用高硅生铁代替废钢,进而提高整体入炉料平均硅,同时开吹加入提温剂平衡总体热量,避免热量过于偏低;本发明提出在冶炼过程中加入高效化渣剂,提高过程化渣效果有效抑制过程金属喷溅。本发明解决了低硅铁水实际冶炼过程中容易造成化渣不良、脱磷困难、钢水过氧化、粘烟罩、粘炉口、粘枪、烧枪、炉衬侵蚀严重等一系列问题,稳定了生产操作。
一种低硅高磷铁水转炉冶炼方法.pdf
本发明涉及冶金技术领域,尤其涉及一种低硅高磷铁水转炉冶炼方法,其包括如下操作:转炉点火成功后,将氧枪枪位降到基本枪位1.3m,加入第一批渣料,第一批渣料包括活性石灰总量的2/3、轻烧白云石的全部、硅石全部及烧结矿,活性石灰按炉渣碱度控制在2.6‑3.0进行配加,硅石按铁水含硅0.35%等量配加,烧结矿按300‑500kg/炉;氧枪控制采用变枪变压法,前期枪位1.3m,流量24000m3/h;过程枪位1.4‑1.5m,化渣枪位1.7‑1.8m,氧气流量22000m3/h;后期拉碳枪位1.1m,流量24000
一种采用低硅铁水转炉冶炼低磷钢的方法.pdf
本发明公开了一种采用低硅铁水转炉冶炼低磷钢的方法,所述方法包括以下步骤:1)冶炼炉次开始装料前,根据所冶炼钢种的终点磷含量要求以及铁水成分,确定转炉留渣量,并计算石灰加入总量;2)根据石灰加入量确定双渣前期石灰、矿石加入量;3)开吹后,操作人员根据音频化渣监控到的炉内渣化情况,结合炉口镜头监控到的情况来确定双渣提枪时机;4)提枪后,对炉内吹扫氮气,进行刹铁作业;5)倒渣完毕再次开吹,加入剩余50%的石灰、矿石,造二次渣去磷;6)转炉吹炼至终点提枪,倒炉倒渣。本发明采用双渣控制方法进行操作,转炉终点磷含量基
一种低硅高磷铁水的转炉单渣冶炼方法.pdf
本发明公开了一种低硅高磷铁水的转炉单渣冶炼方法,按照铁水Si≤0.3%和0.3%<Si≤0.5%两个区间对铁水、废钢装入量以及白灰、白云石、铁皮球装入量进行细化控制,冶炼采用“低‑高‑低”枪位控制。本发明的目的是提供一种低硅高磷铁水的转炉单渣冶炼方法,对于低硅高磷铁水的冶炼,对不同的铁水硅含量细化了铁水、废钢的装入量,冶炼过程热量平衡,冶炼温度能够实现平稳控制,同时对不同铁水硅含量的渣料加入量进行了细化,提高了化渣效果,保证了炉渣碱度及氧化性,有效提高了转炉脱磷效果。