
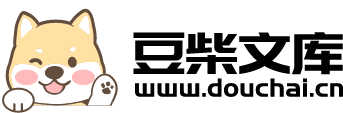
一种赤泥多组份分离与尾渣调质利用的工艺.pdf
静芙****可爱
在线预览结束,喜欢就下载吧,查找使用更方便
相关资料
一种赤泥多组份分离与尾渣调质利用的工艺.pdf
本发明涉及固废资源综合利用领域,公开了一种赤泥多组份分离与尾渣调质利用的工艺,包括将赤泥与调质改性造渣剂按一定比例混合;将混合后的物料滚动成型并进行干燥处理,获取干燥球团;将干燥球团与焦炭置入多功能熔炼炉还原,通过气相分离碱金属及重金属等,通过液相分离铁液。将炉内剩余高温熔渣通过离心或喷吹法制备矿棉、岩棉,或通过模板析晶法制备微晶玻璃。本发明提供的赤泥回收利用的方法,实现了固体废弃物赤泥的多组份分离与全组份利用,解决了赤泥利用不充分、污染环境的现状,符合国家提倡的废物利用环保政策,同时处理后可得到的高附加
一种无尾渣综合利用赤泥的方法.pdf
本发明提供了一种无尾渣综合利用赤泥的方法,包括如下步骤:向预处理后的赤泥中加入添加剂和粘结剂,进行混合、造球和烘干,得到赤泥干球;将干球预热焙烧,得到预热球团;向预热球团中加入还原剂进行预还原处理,得到预还原球团;向所得预还原球团中加入还原剂,混合后在电炉内进行熔分处理,得到生铁与熔分渣;将所得熔分渣与碳酸钠、石灰石混合后进行渣改性处理,得到改性渣;将改性渣进行球磨与碱浸,得到碱浸渣和铝酸盐溶液;将碱浸渣进行稀酸浸出脱硅和铝,得到酸浸液和钙钛矿精矿。本发明可实现赤泥中铁、铝、硅和钛等主要有价元素的高效分离
一种梯级回收赤泥中铁钠资源及尾渣全量化利用的方法.pdf
本发明公开了一种梯级回收赤泥中铁钠资源及尾渣全量化利用的方法,将赤泥原料磨细后加入硫酸进行酸浸使Fe、Na溶解;向浸出液中加入过量的氨水获得Fe(OH)
一种赤泥组份分离方法.pdf
一种赤泥组份分离方法,涉及到氧化铝生产过程中废弃物赤泥组份分离方法。其特征在于其分离过程将赤泥在焙烧炉中进行焙烧,焙烧产生的气相进入多个保温凝析罐中逐级进行分离,焙烧的固相采用浸出方法进行提取分离。本发明的方法使有价金属在气相阶段有效地实现了分离,并全部回收了气相物质,全系统为负压操作环境,避免了焙烧过程产生的气体污染。在气相阶段对赤泥组份进行有效的分离,利用凝析点的差异进行气相混合物的分离。从而降低了分离工序的技术难度,大大延伸了焙烧设备的分离效能,将焙烧和分离设备高效地整合为一体,简化工艺流程,提高分
一种利用赤泥高效渣铁分离制备镍硬Ⅰ型铸铁方法.pdf
本发明公开一种利用赤泥高效渣铁分离制备镍硬Ⅰ型铸铁方法,属于金属冶金技术领域,包括如下步骤:先将拜耳法赤泥、红土镍矿混合后,向上述混合物中添加焦粉、生石灰混合均匀,再将混料预热后放入炉中进行加热还原,得到铁合金;将铁合金添加镍、铬制备成镍硬铸铁,再进行低温回火处理,然后出炉空冷即可。实现了拜耳法赤泥的有效治理,减低成本,对环境友好,且得到的成品镍硬铸铁的组织特点符合镍硬Ⅰ型铸铁组织标准。