
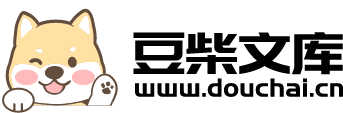
高炉、炉缸及炉壳与冷却壁间灌浆封堵炉基煤气泄漏方法.pdf
Ch****49
在线预览结束,喜欢就下载吧,查找使用更方便
相关资料
高炉、炉缸及炉壳与冷却壁间灌浆封堵炉基煤气泄漏方法.pdf
本发明公开了高炉、炉缸及炉壳与冷却壁间灌浆封堵炉基煤气泄漏方法,其中高炉炉缸包括筒状的炉壳、位于所述炉壳内侧的高炉冷却壁和填充在所述炉壳与所述高炉冷却壁之间的压浆填充料,所述高炉冷却壁包括多个上下叠置的冷却壁筒,且相邻所述冷却壁筒的间隙中通过连接料填充,至少一组相邻的所述冷却壁筒之间的环形间隙为密封间隙,所述密封间隙靠近所述炉壳的一侧环向填充有向外夯实的密封填充料,所述密封填充料外侧与所述炉壳内壁相抵,内侧延伸至所述冷却壁筒外侧面的内侧,所述密封间隙位于所述密封填充料的外侧部分通过所述连接料填充连接。
一种封堵高炉炉基煤气泄漏的方法.pdf
本发明公开了一种封堵高炉炉基煤气泄漏的方法,所述方法包括以下步骤:1):高炉休风期间,在高炉炉基处的混凝土平台上沿炉壳一周开大槽,大槽底部开设小槽,小槽内设置密封圈,采用预埋板圈压紧密封圈,并将预埋板圈覆盖在小槽上且固定在大槽的底部;2):在预埋板圈与炉壳之间固定设置密封板圈,使预埋板圈、混凝土平台、炉壳、密封板圈围成一个封闭空间,在密封板圈上设置连通封闭空间的灌浆装置;3)、在预埋板圈与密封板圈之外的大槽内灌入泥浆,同时通过灌浆装置向密封空间内灌入灌浆料即完成对炉基与混凝土平台之间的煤气泄漏点进行封堵。
高炉炉缸冷却壁的传热分析.docx
高炉炉缸冷却壁的传热分析高炉炉缸冷却壁的传热分析摘要:高炉是冶金工业中常用的设备,其内部炉缸冷却壁的传热效果直接影响到高炉的工作效率和寿命。本论文通过分析高炉炉缸冷却壁的传热机制和影响因素,探讨了如何提高传热效率的方法和技术,以期提高高炉的工作效率和寿命。1.引言高炉是冶金工业中重要的设备,用于将冶炼矿石转化为熔融金属的工艺过程。在高炉的内部,炉缸冷却壁起到了关键的作用,它既能保护高炉内部结构不受高温和熔融物的侵蚀,同时也能提高高炉的工作效率和寿命。因此,炉缸冷却壁的传热分析是提高高炉性能的关键问题。2.
高炉炉壳冷却壁安装系统及安装方法.pdf
本发明公开了一种高炉炉壳冷却壁安装系统及安装方法,该系统包括可调顶紧装置、位于炉壳内且与炉壳中心轴垂直的操作平台和能同时吊装多块冷却壁的吊架,可调顶紧装置包括伸缩杆,伸缩杆一端能360度旋转的铰接在操作平台上、中部通过支座可滑动的支撑在操作平台上、另一端固定有顶紧架,伸缩杆的铰接点位于炉壳中心轴上,顶紧架上设有多个联动的液压顶,顶紧架上的液压顶与吊架上的冷却壁一一对应。该系统能同时安装多个冷却壁,安装精度高,安装效率高。
基于高炉冷却壁水温差的炉缸炉底侵蚀分析.docx
基于高炉冷却壁水温差的炉缸炉底侵蚀分析摘要为了分析高炉冷却壁水温差对炉缸炉底侵蚀的影响,本文对高炉内的温度变化和水冷壁的工作情况进行了分析。通过对高炉内火焰温度、炉壳温度和冷却壁水温的监测,发现冷却壁水温差较大时容易引起炉壳的破裂和炉缸、炉底的侵蚀。同时,结合实际运行情况,本文提出了改善高炉冷却壁水温差的方法,并探讨了其实际应用效果。结果表明,合理地调整冷却壁水的供水和回水温度,可以有效地降低炉缸炉底侵蚀的程度,提高高炉的生产效率和降低维护成本。关键词:高炉;炉缸炉底侵蚀;冷却壁水温差;改善方法;应用效果