
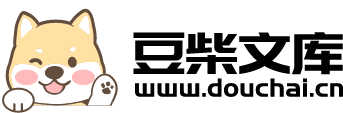
一种铸锭炉用复合碳碳盖板、及其制备方法和用途.pdf
An****99
亲,该文档总共11页,到这已经超出免费预览范围,如果喜欢就直接下载吧~
相关资料
一种铸锭炉用复合碳碳盖板、及其制备方法和用途.pdf
本发明涉及一种铸锭炉用复合碳碳盖板,所述碳碳盖板包括碳碳基体和微粉材料层,以及设置在所述碳碳基体和微粉材料层之间的微粉碳材料混合层;所述微粉碳材料混合层为渗透有微粉材料的碳材料。本发明将所述微粉材料渗透到碳碳盖板内部,形成微粉碳材料混合层,进而微粉材料与碳碳盖板间具有良好的结合性,不易脱落;微粉材料覆盖在微粉碳材料混合层表面,形成微粉材料层,所述微粉材料层可以起到隔离的作用,在用作多晶硅铸锭炉的盖板时,可以起到阻碍硅蒸汽和碳碳盖板发生反应的作用,进而有效防止碳化硅的生成,提高盖板的强度。
一种多晶硅铸锭炉用碳碳盖板的制备方法.pdf
本发明公开了一种多晶硅铸锭炉用碳碳盖板的制备方法,包括如下步骤:1.将碳纤维编织成双向碳布;2.对双向碳布进行高温预处理以提高碳纤维的表面活性;3.将预处理过的双向碳布制备成酚醛树脂预浸料;4.通过挤压的方法将预浸碳布丝束展宽;5.预浸碳布铺层并热压固化成型得到树脂基模压板;6.碳化处理;7.树脂浸渍‑碳化工艺增密;8.石墨化处理;9.表面涂层处理;10.机械加工。与现有技术相比,本发明具有盖板产品层间强度高、纤维含量高、平整性好、使用寿命长等特点,大大增强盖板产品的刚度,有效改善板材使用变形问题,可提高
一种光伏铸锭炉用碳碳复合材料的保护层及其制备方法.pdf
本发明提供了一种光伏铸锭炉用碳碳复合材料的保护层及其制备方法,保护层包含下述质量份数的原料:石墨胶50~70份,天然沥青10~20份,混合乳液20~30份。石墨胶的原料包括石墨粉、丙酮、热固性树脂。混合乳液的原料包括:乙醇、液氨、氢氧化钠、十二烷基硫酸盐、质量分数为0.2%~10%的溴盐类离子液体。该保护层的制备方法包括以下步骤:石墨固体粉碎得石墨粉;将石墨粉、丙酮、热固性树脂混合制备石墨胶;将乙醇、液氨、氢氧化钠、十二烷基硫酸盐、溴盐类离子液体混合制备混合乳液;将石墨胶、天然沥青、混合乳液混合;压制成片
一种单晶炉碳/碳复合材料隔热屏及其制备方法.pdf
本发明提供一种多晶硅还原炉用碳/碳材料隔热屏,具体公开了一种单晶炉碳/碳复合材料隔热屏及其制备方法。此隔热屏结构为拼接结构,包括屏上圈与屏下圈及碳条,屏上圈与下圈之间用一定宽度的碳条与碳螺钉,组合拼装成一个近似于圆的多边形;根据所需隔热屏的外径,内径及高度尺寸,确定上圈及下圈的规格,其中上圈及下圈的内径设计为隔热屏的内径,其外径为内径尺寸加10~40mm;高度一般设计为10~50mm,且在上圈下部及下圈上部为台阶面,上面根据圆周尺寸均布一定数量的螺纹孔,螺纹孔规格为M5~M24,孔间距为孔径的2~4倍;碳
多晶硅铸锭炉用的复合隔碳涂层以及制备方法、石墨护板、多晶硅铸锭炉.pdf
本发明公开了一种多晶硅铸锭炉用的复合隔碳涂层,用于涂覆在铸锭炉内的碳材料器件表面,防止碳污染,其特征在于:所述复合隔碳涂层包括涂覆在器件表面的由金属钨或金属钼构成的第一涂层,以及涂覆在第一涂层上的第二涂层,所述第二涂层为氮化硅层或者由氮化硅层与氧化硅层构成的叠层,第一涂层厚度为0.02-300微米,第二涂层厚度为0.02-300微米。本发明还公开了一种制备所述的复合隔碳涂层的方法;同时,本发明还公开了包含所述的复合隔碳涂层的石墨护板以及多晶硅铸锭炉。本发明通过在多晶铸锭炉内的碳材料器件表面涂覆所述复合隔碳