
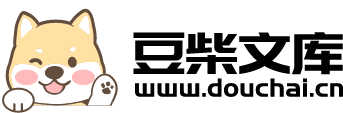
一种耐硫变换工艺流程优化方法.pdf
猫巷****傲柏
在线预览结束,喜欢就下载吧,查找使用更方便
相关资料
一种耐硫变换工艺流程优化方法.pdf
本发明公开一种耐硫变换工艺流程优化方法,涉及耐硫变换工艺技术领域,主要结构包括原料气分离器、煤气预热器、预变换炉、第一淬冷过滤器、蒸汽混合器、第一变换炉、蒸汽过热器、第二淬冷过滤器、第二变换炉、第三淬冷过滤器、第三变换炉、废锅、第一脱盐水预热器、第二脱盐水预热器、第一变换气分离器、变换气水冷器和第二变换气分离器。通过优化工艺流程,降低变换系统阻力降,为装置提升负荷,提高合成氨产量创造了条件,提高预变炉催化剂使用寿命,降低了变换系统管道泄漏情况,降低蒸汽消耗量。
耐硫变换催化剂及其制备方法.pptx
汇报人:目录PARTONE金属氧化物催化剂硫化物催化剂复合催化剂PARTTWO溶胶凝胶法沉淀法浸渍法微乳液法PARTTHREE原料的种类和纯度反应温度和时间催化剂的负载量和活性组分含量PARTFOUR溶胶凝胶法的优缺点沉淀法的优缺点浸渍法的优缺点微乳液法的优缺点PARTFIVE提高催化剂的活性、选择性和稳定性降低制备成本和简化制备过程开发新型的制备方法和工艺PARTSIX耐硫变换催化剂在化工领域的应用在环境保护和能源利用领域的应用前景在新材料的开发和应用方面的展望THANKYOU
耐硫变换催化剂的预硫化方法.pdf
本发明涉及一种耐硫变换催化剂的预硫化方法,属于催化剂技术领域。本发明包括以下步骤:(1)取硫代硫酸铵溶于水中,作为溶液A;取氧化态钴钼系耐硫变换催化剂按照其吸水率进行等量浸渍,并烘干;(2)将硫磺溶于CS<base:Sub>2</base:Sub>溶液中,作为溶液B;将烘干后的催化剂放入溶液B中进行第二次等量浸渍;(3)将浸渍完成的催化剂放入预硫化处理装置中,在含氢气的氮气环境中,先升温,再恒温,然后升温,恒温,将温度降至常温,得到含部分活性硫化物的耐硫变换催化剂。本发明简单易行,在催化剂内孔形成单质硫的
耐硫变换催化剂的预硫化方法.pdf
本发明涉及一种耐硫变换催化剂的预硫化方法,属于催化剂技术领域。本发明包括以下步骤:(1)取硫代硫酸铵溶于水中,作为溶液A;取氧化态钴钼系耐硫变换催化剂按照其吸水率进行等量浸渍,并烘干;(2)将硫磺溶于CS<base:Sub>2</base:Sub>溶液中,作为溶液B;将烘干后的催化剂放入溶液B中进行第二次等量浸渍;(3)将浸渍完成的催化剂放入预硫化处理装置中,在含氢气的氮气环境中,先升温,再恒温,然后升温,恒温,将温度降至常温,得到含部分活性硫化物的耐硫变换催化剂。本发明简单易行,在催化剂内孔形成单质硫的
一种多级调整水气比的耐硫变换方法及装置.pdf
本发明属于煤化工领域,公开了一种多级调整水气比的耐硫变换方法及装置。该方法首先通过使用自产蒸汽全部或部分用于配汽初步调节水气比,然后原料气换热升温后通过喷淋减温器与喷入的锅炉给水混合实现第二次调节水气比,接着原料气通过保护床反应器后被分为三路,通过调整三路比例第三次调节水气比,之后通过减温塔调节二级及三级耐硫变换反应器的水气比,多级调节水气比,在保持装置平稳操作的前提下,减少了蒸汽的消耗,更好的调控一级耐硫变换反应器入口温度,更好的保证了催化剂的寿命。