
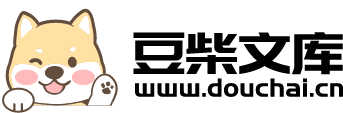
一种铝基复合材料精炼装置以及制备方法.pdf
代瑶****zy
在线预览结束,喜欢就下载吧,查找使用更方便
相关资料
一种铝基复合材料精炼装置以及制备方法.pdf
本发明属于铝基复合材料的制备技术领域,具体为一种铝基复合材料精炼装置以及制备方法,包括精炼炉,内设置有多级搅拌机构,多级搅拌机构包括转轴,在精炼炉上方并与转轴连接的驱动机构,转轴下方连接有多级搅拌转子,多级搅拌转子为三级结构转子;包括位于上方的第一级叶片,位于中部的第二级叶片和位于底部的第三级叶片,第一级叶片和第三级叶片为螺旋型叶片,第二级叶片为柱状;精炼炉上配合设置有真空系统,精炼炉下方设有电磁阀;铝合金熔体内通过气体喷吹后送入精炼炉中,采用多级搅拌转子进行搅拌后进行铝合金铸造,本发明通过高速剪切搅拌作
一种铝基复合材料压力浸渗制备装置及制备方法.pdf
本发明属于金属基复合材料制备领域,公开了一种铝基复合材料压力浸渗制备装置及制备方法。所述装置包括机架,多个升降机构、电阻炉、浸渗压力控制系统、真空控制系统和电控机箱,每个升降机构可通过独立的炉管升入电阻炉内部。本发明的装置采用多根炉管的设置,提高了电阻炉炉膛内部空间的使用率,提高了复合材料的制备效率,多个复合材料试样在相同条件下同时制备,提高了复合材料制备的稳定性,保证了复合材料性能的一致性。并可根据需要在不同炉管内实现不同压力浸渗的同时制备。
一种制备铝基复合材料的简易装置.pdf
本发明涉及工业材料制造装置领域,尤其是一种制备铝基复合材料的简易装置,包括加压管、储料管、压料杆及加压件,所述加压管为内螺纹管,所述加压管一端与所述加压件螺纹连接,另一端通过连接件与所述储料管接驳;所述储料管包括储料仓、固定件及开关盖,所述储料仓与所述储料管为相嵌结构;所述压料杆嵌插于所述加压管及所述储料管内,所述压料杆一端设有压料件。本发明的制备铝基复合材料的简易装置能够可以在无专门的热压烧结炉的情况下,通过加热就能够制备出致密度高的铝基复合材料,而且能够通过更换储料仓及压料件制备出不同形状及大小的铝基
一种铝基复合材料的制备方法.pdf
本发明公开了一种铝基复合材料的制备方法,涉及铝基复合材料领域。本发明的操作方法是将金刚石或金刚石与碳化硅混合粉末颗粒,氟钛酸钾,或氟锆酸钾、或氟硼酸钾、或氟硅酸钾、或者氟钽酸钾,将上述两种或几种粉料混合均匀。将炉中铝熔化,升温至660℃?1500℃后将混合粉状原料加入炉中充分搅动熔液保温后,对熔液扒渣后,充分搅动熔液后的熔液浇铸成各种产品。本发明有效地提高了铝基复合材料性能,工艺简单方便操作成本低,可以工业化生产。
铝基复合材料的制备方法.docx
铝基复合材料的制备方法随着现代航空、汽车、电子等行业的不断发展,对材料的性能要求也越来越高,因此研究和开发新型的材料成为了亟待解决的问题。铝基复合材料作为一种轻质、高强度、耐腐蚀的先进材料,近年来受到了广泛关注。铝基复合材料的制备方法有很多种,如粉末冶金法、热爆炸法、熔覆法、机械合金化等。下面将重点介绍两种常用的制备方法:热压法和搅拌摩擦焊接法。1.热压法热压法是一种通过高温高压使铝基复合材料熔合在一起的方法。其制备过程如下:(1)材料准备:将铝及其他复合材料加工成粉末状,并按一定比例混合。(2)热压成型