
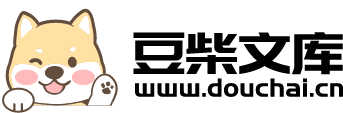
一种异型孔去毛刺及孔金属化的方法.pdf
鸿朗****ka
在线预览结束,喜欢就下载吧,查找使用更方便
相关资料
一种异型孔去毛刺及孔金属化的方法.pdf
本发明提供一种异型孔去毛刺及孔金属化的方法,本发明通过微腐试剂保证孔口毛刺被完全除去,解决了后工序制作过程中干膜被刺破导致孔内无铜或孔内形成铜丝等品质隐患的问题。本发明中所用的微腐试剂不影响线路板性能,去除毛刺效果好,且蒸发速率快,不会影响后续加工,可提高孔口毛刺的处理效率。
一种改善异型槽孔孔内毛刺的方法.pdf
本发明提供一种改善异型槽孔孔内毛刺的方法,通过本发明异型槽孔孔内毛刺加工方法的改善后,异型槽孔孔内毛刺不良率降至10%,提高了产品的质量,节约了原料。
去Φ2孔毛刺交叉孔去毛刺纤维油石刷文件.docx
EZFINICross-HoleDeburringToolEZFINI交叉孔去毛刺纤维油石刷适用于交叉孔去毛刺及盲孔底部表面抛光的自动化工艺。最大长度可达170mmIdealfortheAUTOMATIONofcross-holedeburringandbottomsurfacefinishingofdead-endholes.AddedLongShaft(Fulllength170mm)特性Features氧化铝纤维线材制成的磨棒提供了强力的顶端研磨能力离心力使磨棒充分散开,可有效的去除交叉孔中的毛刺精
一种缸体孔去毛刺装置.pdf
本实用新型提供了一种缸体孔去毛刺装置,属于机械技术领域。一种缸体孔去毛刺装置,包括放置缸体的放置机构和去除缸体孔毛刺的打磨机构,其特征在于,所述放置机构包括放置台,所述放置台上开设有四条滑槽,四条所述滑槽依次相连且垂直,所述滑槽上滑动连接有若干滑箱,四条所述滑槽外分别设置有与之一一对应的第一推杆电机,所述第一推杆电机的推杆能够带动滑箱沿滑槽移动;所述打磨机构包括第二推杆电机,所述第二推杆电机的推杆上固定连接有驱动电机,所述驱动电机的输出轴上可拆卸连接有打磨组件。本实用新型具有可根据需要去毛刺缸体孔的大小快
一种阀体内孔去毛刺装置.pdf
本发明公开了一种阀体内孔去毛刺装置,工作台一端固定有轴承座,轴承座座孔内设有转轴,电机的动力通过带轮传送至转轴,转轴又通过联轴器将动力传送给设于联轴器轴孔内的毛刷,带动毛刷转动;工作台另一端设有导轨,滑板通过其底部设有的凸块卡合置于导轨上,并沿导轨作左右往复运动;滑板底部还固定连接有滑座,滑座又与液压油缸相连,在动力装置的控制下,液压油缸带动滑座、滑板及置于滑板上的工件作左右往复运动。本发明通过选择电机来传送动力,带动毛刷转动,又通过利用动力装置来操纵液压油缸,带动阀体工件作左右往复运动,实现阀体内孔去毛