
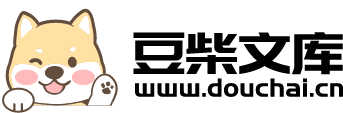
吸附柱及氢氮分离系统.pdf
An****70
亲,该文档总共14页,到这已经超出免费预览范围,如果喜欢就直接下载吧~
相关资料
吸附柱及氢氮分离系统.pdf
本发明公开一种吸附柱,包括壳体,还包括:膜组件,设置于所述壳体内部,且其包括若干沿所述壳体的轴向间隔设置的膜分离单元;所述膜分离单元包括依次连通的引导段和膜分离段;吸附剂层,填充于相邻膜分离单元之间和膜分离单元与壳体内壁之间。本发明还公开了使用该吸附柱作的氢氮分离系统。本发明公开的吸附柱,将膜分离技术和变压吸附技术一体化,其系统结构紧凑,占地面积小,避免在两种方法连用时因为管道过多引起的气体损耗,成本低廉适合中小规模的气体制备工艺的后续气体提纯,同时兼顾最终得到的气体的收率和纯度,结构灵活,方便拆卸,泛用
变压吸附制氢系统.pdf
本发明公开了一种变压吸附制氢系统,包括吸附塔、顺放装置、逆放装置和抽真空装置,吸附塔为多台,每个吸附塔具有底部管线和顶部管线,底部管线用于导入原料气,顶部管线用于输出产品气;顺放装置与顶部管线连通,以收集顺放过程中的顺放气;逆放装置与底部管线连通,以将吸附塔吸附的杂质气体解吸形成逆放气;抽真空装置与底部管线连通,以将吸附塔内抽真空。此技术主要通过改变吸附剂再生工艺,采用真空再生法,从而使吸附剂在负压下将吸附的杂质气体完全解吸,提高吸附剂的吸附能力,进而使吸附剂的再生效率和氢气回收率均有效提高。解决了现有技
选择性吸附氧气的氮氧分离吸附剂研究的开题报告.docx
选择性吸附氧气的氮氧分离吸附剂研究的开题报告一、研究背景和意义随着经济和人口的持续增长,能源需求和环境污染问题逐渐成为世界上最严重的问题之一。其中,石油和天然气等化石能源的消耗已经引起了全球气候变化和环境污染等问题。因此,开发可持续、清洁的能源已经成为世界各国的共同任务。氢能作为一种绿色、清洁、高效的能源,能够较好地解决环境和能源之间的矛盾,因此备受关注。然而,氢气的制备与运输、储存仍然存在技术难题。其中,将氢气从混合气体中提取出来就显得更为关键。由于氢气和氧气具有相似的分子大小和极性,在传统的物理或化学
用于核酸提取的吸附柱及采用吸附柱的吸附组件.pdf
本实用新型公开了一种用于核酸提取的吸附柱及采用吸附柱的吸附组件,吸附柱包括柱体(1)和匹配盖合的盖体(2)以及用于连接的连接带(3),所述柱体(1)的外壁上设有第一磨砂部(101)和/或所述盖体(2)的盖面外侧为磨砂层;所述柱体(1)的外壁上分布有用于固定连接收集管(7)的凸棱(102)且凸棱(102)沿柱体(1)的长度方向延伸。吸附组件包括套设在柱体(1)外的收集管(7),所述收集管(7)上设置的第三凸环(702)能够与柱体(1)外壁上的凸棱(102)过盈配合以紧固连接吸附柱和收集管(7)。本实用新型的
一种轧钢退火炉的氮氢保护气分离系统及方法.pdf
本发明提供了一种轧钢退火炉的氮氢保护气分离系统及方法,该系统包括连续退火炉、冷却器、放散烟囱、催化脱氧器、吸附再生式干燥装置、膜分离器;连续退火炉的保护气排出口通过分支管道分别连接冷却器和放散烟囱,分支管道上设有控制阀门,冷却器的出气口与催化脱氧器的进气口相连,催化脱氧器的出气口与吸附再生式干燥装置的进气口相连,吸附再生式干燥装置的出气口与膜分离器的进气口相连,膜分离器内设有中空纤维聚砜复合膜。该发明将氮氢保护气经降温、除氧、干燥处理后,通过膜分离技术对氮氢保护气进行氮氢分离,得到富氢混合气可再次回收利用