
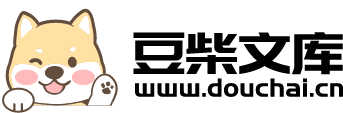
基于高磷铁矿金属化产物高温熔分制备低磷铁水的方法.pdf
白真****ng
亲,该文档总共17页,到这已经超出免费预览范围,如果喜欢就直接下载吧~
相关资料
基于高磷铁矿金属化产物高温熔分制备低磷铁水的方法.pdf
本发明提供一种基于高磷铁矿金属化产物高温熔分制备低磷铁水的方法,包括步骤:制备孔隙化处理的高磷铁矿金属化产物;脱磷剂和熔分添加剂制备;将经孔隙化处理的高磷铁矿金属化产物与脱磷剂、熔分添加剂分批次加入矿热炉中进行高温熔分;出渣和出铁。本发明提出的基于高磷铁矿金属化产物的高效熔分制备低磷铁水的方法,具有磷脱除率高、铁回收率高、热效率高和铁水碳含量低的特点。
高磷铁矿制备低磷铁水的方法及装置.pdf
本发明提供一种高磷铁矿制备低磷铁水的方法及装置,包括如下步骤:将高磷铁矿、还原剂和熔剂按照预设比例进行配料混合处理,得到均匀的混合物料;将混合物料加入至电热还原炉中,在1450℃~1650℃的熔炼温度下对混合物料进行还原熔炼处理,得到高磷铁水、炉渣和熔炼烟气;将高磷铁水送入脱磷炉中,向脱磷炉内加入冷却剂和脱磷剂,并通过浸没式喷枪向高磷铁水中吹入氧化性气体,对高磷铁水进行脱磷处理,得到低磷铁水、含磷炉渣和脱磷烟气。利用本发明能够解决现有高磷铁矿制备低磷铁水的技术存在除磷效果不佳、工业成本高、周期长、达不到钢
利用富氧顶吹熔融还原高磷铁矿制取低磷铁水的方法.pdf
本发明公开了在富氧顶吹的条件下,用高磷铁矿作原料、煤粉作还原剂、石灰石或白云石作熔剂生产铁水。工艺步骤为:将炉料高磷铁矿、白云石、石灰和还原煤破碎;按照碱度R为1.0~2.0,内配碳比C/O为0.9~1.3配比混匀、预热;由氮气作为载气喷吹炉料从炉侧进入熔融还原炉,在富氧顶吹的条件下生产磷含量相对较低的铁水,其铁水和炉渣定期分别由出铁口和排渣口放出。高温烟气除尘、二次燃烧,利用余热发电,并进行炉外脱磷和脱硫。本发明克服了传统方法难以冶炼高磷铁矿的难题,对原料要求简单,建设成本低,高温炉气的余热和化学能可以
低硅高磷铁水冶炼低磷钢双渣去磷的方法.pdf
本发明涉及炼钢技术领域,具体而言,涉及低硅高磷铁水冶炼低磷钢双渣去磷的方法,通过在添加碳粉和矿石,再吹入氮气,以便于增加炉内钢渣中的气体含量,以形成泡沫渣,泡沫渣具有很厚的渣层,液珠在泡沫渣中停留时间长,有利于磷的去除,以使终点磷含量满足要求。
高磷还原铁生产低磷铁水的方法及装置.pdf
本发明提供一种高磷还原铁生产低磷铁水的方法及装置,包括如下步骤:将高磷还原铁加入至脱磷炉中,向脱磷炉中加入氧化剂和脱磷剂,得到位于脱磷炉中的待熔化物料;通过浸没式喷枪向脱磷炉内喷入富氧空气和燃料,对待熔化物料进行熔化处理,得到熔化铁水物料;控制富氧空气中的空气的过剩系数为1.0~2.0,使燃料燃烧后得到的气体为弱氧化性气体,并通过弱氧化性气体对熔化铁水物料进行脱磷处理,当终点渣的二元碱度为2.0~5.0时,完成脱磷处理,得到低磷铁水、含磷炉渣和高温烟气。利用本发明能够解决现有高磷还原铁生产低磷铁水的技术存