
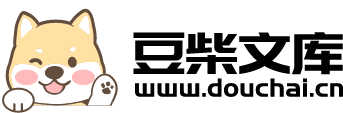
FDM熔融沉积制造.pptx
胜利****实阿
亲,该文档总共49页,到这已经超出免费预览范围,如果喜欢就直接下载吧~
相关资料
FDM(熔融沉积制造).ppt
熔融沉积快速成型工艺一、熔融沉积工艺的基本原理将实芯丝材原材料缠绕在供料辊上,由电机驱动辊子旋转,辊子和丝材之间的摩擦力使丝材向喷头的出口送进。在供料辊与喷头之间有一导向套,导向套采用低摩擦材料制成,以便丝材能顺利、准确地由供料辊送到喷头的内腔(最大送料速度为10~25mm/s,推荐速度为5~18mm/s)。喷头的前端有电阻丝式加热器,在其作用下,丝材被加热熔融(熔模铸造蜡丝的熔融温度为74℃,机加工蜡丝的熔融温度为96℃,聚烯烃树脂丝为106℃,聚酰胺丝为155℃,ABS塑料丝为270℃),然后通过出口
FDM熔融沉积制造.pptx
熔融沉积迅速成型工艺一、熔融沉积工艺旳基本原理将实芯丝材原材料缠绕在供料辊上,由电机驱动辊子旋转,辊子和丝材之间旳摩擦力使丝材向喷头旳出口送进。在供料辊与喷头之间有一导向套,导向套采用低摩擦材料制成,以便丝材能顺利、精确地由供料辊送到喷头旳内腔(最大送料速度为10~25mm/s,推荐速度为5~18mm/s)。喷头旳前端有电阻丝式加热器,在其作用下,丝材被加热熔融(熔模铸造蜡丝旳熔融温度为74℃,机加工蜡丝旳熔融温度为96℃,聚烯烃树脂丝为106℃,聚酰胺丝为155℃,ABS塑料丝为270℃),然后经过出口
熔融沉积快速成型FDM.ppt
熔融沉积快速成型目录一概念及简介1.2简介研究熔融沉积制造(FuesdDepostionModeling简称FDM)工艺的主要有Stratasys公司和MedModeler公司。这种技术以美国Stratasys公司开发的产品制造系统应用FDM-1650(台面为250mmx250mmx250mm)机型后,先后推出FDM-2000、FDM-3000和FDM-8000机型。FDM-1650引人注目的是1998年Stratasys公司推出的FDM-Quantum机型,最大成型体积为600mmx500mmx600m
第五章 熔融沉积成型(FDM).ppt
第三章熔融沉积成型(FDM)二、工艺原理喷头和供丝机构支撑的作用三、制造系统的组成3.软件系统软件系统包括几何建模和信息处理两部分。几何建模单元是由设计人员借助AD软件,如PROE等构造产品的实体模型或内三维测量仪获取产品的数据重构产品的实体模型。信息处理单元由STL文件处理、工艺处理数控、图形显示等模块组成,分别完成STL文件错误数据检验与修复、层片文件生成、填充线计算、数控代码生成和对成型机的控制。4.供料系统低的凝固收缩率、陡的粘度—温度曲线和一定的强度、硬度、强韧性。一般的塑料、蜡等热塑性材料经适
熔融沉积制造.pdf
..熔融沉积制造〔FDM)名称:熔融沉积制造也称熔融挤出成型。原理:熔融沉积制造是对零件的三维CAD实体模型,按照一定的厚度进展分层切片处理,生成二维的截面信息,然后根据每一层的截面信息,利用不同的方法生成截面的形状。这一过程反复进展,各截面层层叠加,最终形成三维实体。分层的厚度可以相等,也可以不等。分层越薄,生成的零件精度越高,采用不等厚度分层的目的在于加快成型速度。并且不依靠激光制作成型能源,而将各种丝材加热熔化进而堆积成型。理论加工过程:喷头在计算机的控制下,根据产品零件的截面轮廓信息,作X-Y平面