
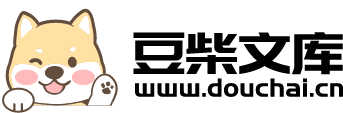
原液着色纤维产业十三五发展路径.docx
胜利****实阿
在线预览结束,喜欢就下载吧,查找使用更方便
相关资料
原液着色纤维产业十三五发展路径.docx
原液着色纤维产业“十三五”发展路径金剑+李鑫+王颖+廉志军+邱志成项目背景随着人们环保意识的日益增强,全球低碳经济的发展,化纤纺织行业为寻找更为清洁的染色方法以解决染色过程中能源消耗大、废水产生多,环境污染严重等问题,开发了纺前着色即原液着色技术。原液着色纤维是指在纺丝溶液或熔体中加入着色剂,经纺丝过程得到的有色纤维,也称为无染纤维或纺前染色纤维。原液着色纤维加工成纺织品时省去染色工序,避免产生大量的印染废水,减少CO2排放,具有显著的环境友好特征。目前国内有中国纺织科学研究院、仪征化纤等少数科研机构与企
原液着色纤维2018春夏流行趋势解析.docx
原液着色纤维2018春夏流行趋势解析原液着色纤维2018春夏流行趋势解析引言:随着时代的发展和人们对时尚的关注,纺织品行业也在不断创新和发展。纺织品的颜色选择对整体服装的效果起着决定性的作用。在2018年的春夏季节,原液着色纤维成为了一种流行趋势,这种趋势是根据消费者的需求和时尚设计师的创意所产生的结果。本文将分析原液着色纤维在2018春夏的流行趋势,并探讨其原因和对纺织品行业的影响。一、原液着色纤维的定义和特点原液着色纤维是指在纤维生产的过程中将颜料直接添加到纤维原料中进行染色的一种技术。与传统的染色工
聚酰胺纤维原液着色母粒的制备及性能研究.docx
聚酰胺纤维原液着色母粒的制备及性能研究聚酰胺是一种重要的合成纤维,具有优异的物理和化学性质,被广泛应用于纺织、医疗、航空航天等领域。为了改善聚酰胺纤维的颜色,研究人员开始着色母粒的制备及性能研究。本文将详细介绍聚酰胺纤维着色母粒的制备方法,以及其对纤维性能的影响。着色母粒是一种由颜料和添加剂组成的固体颗粒,其主要作用是在纤维制备过程中加入,以实现纤维的着色。聚酰胺纤维的着色母粒制备主要包括颜料选择、配方设计、颜料分散和固化等步骤。首先,根据所需颜色的要求,选择合适的颜料。然后,通过调整颜料与添加剂的配比,
原液着色功能性纤维及在袜品领域的应用.docx
原液着色功能性纤维及在袜品领域的应用随着人们健康意识的增强和生活水平的提升,人们对于服装材质和健康功能的要求也越来越高。原液着色功能性纤维,作为新型材料,因其具有耐磨损、耐洗涤、颜色持久、环保等特点受到世人的广泛青睐。本文将主要探讨原液着色功能性纤维及其在袜品领域的应用。一、原液着色功能性纤维的概述原液着色功能性纤维是一种采用化学物质直接将颜色染入纤维内部的技术,与传统的染色方法相比,其颜色更鲜艳、持久、无挂色、不掉色,同时具有抗菌、防紫外线、保温等多种功能。其制造工艺采用封闭式自动化控制生产技术和环保型
聚苯硫醚纤维原液着色母粒的制备及性能研究.docx
聚苯硫醚纤维原液着色母粒的制备及性能研究聚苯硫醚纤维原液着色母粒的制备及性能研究摘要:本研究通过对聚苯硫醚纤维原液着色母粒的制备及性能进行研究,探讨了聚苯硫醚纤维原液着色母粒的制备工艺、颜色稳定性等性能。采用溶液共混法将染料与聚苯硫醚原液进行混合,并进行挤出、干燥等工艺处理,最终制备出着色母粒。结果表明,制备的聚苯硫醚纤维原液着色母粒颜色鲜艳、稳定性好,能够满足聚苯硫醚纤维的着色需求。关键词:聚苯硫醚纤维;着色母粒;制备;性能研究1.引言聚苯硫醚纤维作为一种新型的高分子材料,在航空、航天、电子通信等领域具