
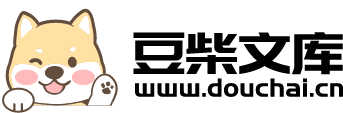
节能与环保论文.docx
大渊****公主
在线预览结束,喜欢就下载吧,查找使用更方便
相关资料
节能与环保论文 节能与环保论文3000字多篇.docx
节能与环保论文节能与环保论文3000字多篇[编辑]节能与环保论文节能与环保论文3000字多篇为的会员投稿推荐,但愿对你的学习工作带来帮助。推荐节能与环保论文篇一环境是人类生产与发展的前提和基础。节约能源,提高能源利用效率,建设资源节约型社会,是全社会成员义不容辞的责任和义务。6月12日至18日全国将开展以“绿色办公、低碳生活”为主题的节能宣传周活动,在此我们发出节能环保建议:1、上下班时尽量乘坐公共交通工具、骑自行车或步行。践行低碳生活从我做起。2、四层之内上下楼不乘电梯走楼梯,环保节能更健康。3、办公室
节能与环保论文.docx
节能与环保论文【摘要】节能环保是实现我国经济可持续发展的必然选择,化工生产行业由于耗能高,污染高,对节能与环保问题应更加重视,不但要创造经济效益,而且要创造环境效益。本文探讨了化工生产中的节能与环保措施。【关键词】化工生产节能环保减排近年来,我国化工行业中,由于高耗能、高污染产品产能增长过快,致使行业产能过剩。我国的一项基本国策就是节能减排,要实现我国经济可持续发展,就必须要求化工行业重视节能与环保,这是实现我国经济可持续发展的必然选择。化工生产行业由于耗能高,污染高,对节能与环保问题应更加重视,不但要创
节能与环保论文.docx
节能与环保论文导语:当代,论文常用来指进行各个学术领域的研究和描述学术研究成果的文章,简称之为论文。下面由小编为大家整理的节能与环保论文,希望可以帮助到大家!【摘要】节能环保是实现我国经济可持续发展的必然选择,化工生产行业由于耗能高,污染高,对节能与环保问题应更加重视,不但要创造经济效益,而且要创造环境效益。本文探讨了化工生产中的节能与环保措施。【关键词】化工生产节能环保减排近年来,我国化工行业中,由于高耗能、高污染产品产能增长过快,致使行业产能过剩。我国的一项基本国策就是节能减排,要实现我国经济可持续发
节能与环保论文.docx
节能与环保论文节能与环保论文导语:当代,论文常用来指进行各个学术领域的研究和描述学术研究成果的文章,简称之为论文。下面由小编为大家整理的节能与环保论文,希望可以帮助到大家!【摘要】节能环保是实现我国经济可持续发展的必然选择,化工生产行业由于耗能高,污染高,对节能与环保问题应更加重视,不但要创造经济效益,而且要创造环境效益。本文探讨了化工生产中的节能与环保措施。【关键词】化工生产节能环保减排近年来,我国化工行业中,由于高耗能、高污染产品产能增长过快,致使行业产能过剩。我国的一项基本国策就是节能减排,要实现我
节能与环保论文.docx
节能与环保论文导语:当代,论文常用来指进行各个学术领域的研究和描述学术研究成果的文章,简称之为论文。下面由小编为大家整理的节能与环保论文,希望可以帮助到大家!【摘要】节能环保是实现我国经济可持续发展的必然选择,化工生产行业由于耗能高,污染高,对节能与环保问题应更加重视,不但要创造经济效益,而且要创造环境效益。本文探讨了化工生产中的节能与环保措施。【关键词】化工生产节能环保减排近年来,我国化工行业中,由于高耗能、高污染产品产能增长过快,致使行业产能过剩。我国的一项基本国策就是节能减排,要实现我国经济可持续发