
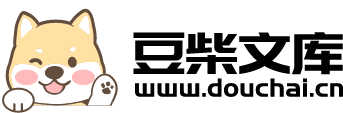
汽柴油加氢装置节能改造及效果分析.docx
依波****bc
在线预览结束,喜欢就下载吧,查找使用更方便
相关资料
汽柴油加氢装置节能改造及效果分析.docx
汽柴油加氢装置节能改造及效果分析总结基于用能的三环节理论[5],加氢装置的节能思路主要包括以下方面:①优化工艺流程和操作,降低装置能耗;②合理调整装置换热流程,减少装置能量输入;③整合公司公用工程管网,杜绝能源的高质低用;④做好設备和管道保温伴热管理,尽量避免不必要散热损失。结合加氢装置实际运行情况,170万t/a汽柴油加氢联合装置实施以下节能改造。3.1汽油加氢装置重沸器凝结水系统改造3.1.1改造背景换热器在石油化工生产中应用广泛,在降低能耗与生产成本中的作用也日益明显[6]。90万t/a汽油加氢装置
汽柴油加氢装置节能改造及效果分析.docx
汽柴油加氢装置节能改造及效果分析总结基于用能的三环节理论[5],加氢装置的节能思路主要包括以下方面:①优化工艺流程和操作,降低装置能耗;②合理调整装置换热流程,减少装置能量输入;③整合公司公用工程管网,杜绝能源的高质低用;④做好設备和管道保温伴热管理,尽量避免不必要散热损失。结合加氢装置实际运行情况,170万t/a汽柴油加氢联合装置实施以下节能改造。3.1汽油加氢装置重沸器凝结水系统改造3.1.1改造背景换热器在石油化工生产中应用广泛,在降低能耗与生产成本中的作用也日益明显[6]。90万t/a汽油加氢装置
汽柴油加氢精制装置节能分析与优化探析.pptx
汽柴油加氢精制装置节能分析与优化探析目录添加章节标题汽柴油加氢精制装置的节能分析装置的能耗组成能耗影响因素分析节能技术应用现状节能潜力评估汽柴油加氢精制装置的优化探析原料油优化操作条件优化催化剂选择与优化装置流程优化汽柴油加氢精制装置的节能技术措施余热回收利用技术高效换热器应用技术装置用能集成优化技术智能化控制技术汽柴油加氢精制装置节能优化实践案例分析案例一:某炼油厂的节能改造实践案例二:某催化剂厂的技术创新实践案例三:某科研机构的节能研究进展案例四:国内外先进装置的节能经验借鉴汽柴油加氢精制装置节能优化
0.6Mta焦化汽柴油加氢装置的技术改造分析.docx
0.6Mta焦化汽柴油加氢装置的技术改造分析摘要随着工业化进程的不断深入,我国石油需求量不断增加。而汽柴油作为交通运输的主要燃料,其重要性不言而喻。然而,传统的汽柴油生产过程中,存在着大量能源浪费和环境污染等问题。因此,本文以一家0.6Mta焦化汽柴油加氢装置的技术改造为研究对象,分析了改造对汽柴油生产过程的影响,并提出了一些改进建议。关键词:汽柴油;焦化;加氢;技术改造;环境污染AbstractWiththedeepeningofindustrialization,thedemandforpetrole
HAZOP分析在汽柴油加氢装置的应用.docx
HAZOP分析在汽柴油加氢装置的应用一、前言随着人们对节能排放的日益重视,汽柴油加氢装置逐渐在炼油厂中得到应用。在加氢装置的工程设计与建设过程中,由于涉及复杂的工艺流程和高压氢气等危险物质,存在很多潜在的安全风险。因此,需要开展HAZOP分析,对加氢装置进行全面、详细的安全评估,指导加氢装置的设计和运行,保障操作人员、设备和环境的安全。二、HAZOP分析的基本概念HAZOP(HazardandOperability)是一种被广泛使用的风险分析方法,可以评估工业生产中不同作业步骤可能造成的危险。HAZOP分