
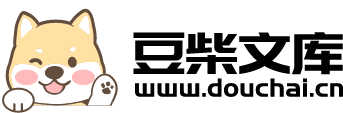
材料失效分析讲义.pdf
文库****品店
在线预览结束,喜欢就下载吧,查找使用更方便
相关资料
材料失效分析讲义.pdf
..材料失效分析讲义失效分析是人们认识事物本质和开展规律的逆向思维和探索,是变失效为平安的根本环节和关键,是人们深化对客观事物的认识源头和途径。根本内容在失效分析中,通常首先将失效分类。从技术角度可按失效机制、失效零件类型、引起失效的工艺环节等分类。从质量管理和可靠性工程角度可按产品使用过程分类。失效率曲线通常称浴盆曲线,它描述了失效率与使用时间的关系。早期失效率高的原因是产品中存在不合格的部件;晚期失效率高的原因是产品部件经长期使用后进入失效期。机械产品中的磨合、电子元器件的老化筛选等就是根据这种失效规
失效模式与影响分析讲义.ppt
FMEA失效模式與影響分析ContentFMEA目的(a)發現和評價設計/過程中潛在的失效及其後果(b)確定能減少或避免潛在失效模式發生的措施(c)將全部過程形成文件FMEA的重點在於設計,目的是防患於未然,本質為工程分析FMEA的分类根据其用途和适用阶段的不同可分为(1)设计阶段FMEA(DFMEA----DesignFMEA)如新产品设计、新工序设计,可预先进行DFMEA尽可能周全地考虑产品规格、制程操作水平、制程能力等因素,使设计符合要求.(2)过程阶段FMEA(PFMEA----ProcessFM
失效模式与影响分析(FMEA)-讲义.ppt
FMEA失效模式與影響分析ContentFMEA目的(a)發現和評價設計/過程中潛在的失效及其後果(b)確定能減少或避免潛在失效模式發生的措施(c)將全部過程形成文件FMEA的重點在於設計,目的是防患於未然,本質為工程分析FMEA的分类根据其用途和适用阶段的不同可分为(1)设计阶段FMEA(DFMEA----DesignFMEA)如新产品设计、新工序设计,可预先进行DFMEA尽可能周全地考虑产品规格、制程操作水平、制程能力等因素,使设计符合要求.(2)过程阶段FMEA(PFMEA----ProcessFM
失效模式与影响分析(FMEA)-讲义.ppt
FMEA失效模式與影響分析ContentFMEA目的(a)發現和評價設計/過程中潛在的失效及其後果(b)確定能減少或避免潛在失效模式發生的措施(c)將全部過程形成文件FMEA的重點在於設計,目的是防患於未然,本質為工程分析FMEA的分类根据其用途和适用阶段的不同可分为(1)设计阶段FMEA(DFMEA----DesignFMEA)如新产品设计、新工序设计,可预先进行DFMEA尽可能周全地考虑产品规格、制程操作水平、制程能力等因素,使设计符合要求.(2)过程阶段FMEA(PFMEA----ProcessFM
FMEA潜在失效模式影响分析讲义.pdf
Tutor:FrankHe讲师:贺昌胜WhatisFMEAFMEA:FailureModeEffectAnalysis潜在失效模式影响分析DFMEA:设计PFMEA:过程SFMEA:系统目的对失效的产品进行分析找出零件组件之失效模式鉴定出它的失效原因研究该项失效模式对系统会产生甚么影响。失效分析找出零组件或系统的潜在弱点提供设计、制造、品保等单位采取可行之对策