
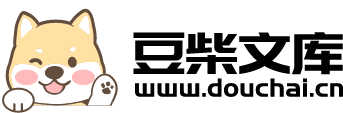
脱硫废水旁路塔雾化蒸发数值模拟.doc
邻家****文章
亲,该文档总共11页,到这已经超出免费预览范围,如果喜欢就直接下载吧~
相关资料
脱硫废水旁路塔雾化蒸发数值模拟.doc
11脱硫废水旁路塔雾化蒸发数值模拟脱硫废水成分复杂难以回用一些电厂已开始采用烟道雾化蒸发处理技术对其进行处理。脱硫废水直接喷入烟道会带来腐蚀、积灰、堵塞等问题设置旁路蒸发塔对脱硫废水进行干燥是一种较好的选择。为研究此项技术以某330MW机组为例通过计算脱硫废水与烟气的热质平衡确定了烟气抽取量建立了物理模型利用数值模拟的方法对烟气流场进行优化对喷嘴布置方式、液滴直径、烟气温度等的选择进行稳态模拟。结果表明:抽取烟气量仅占总烟气量的2.27%烟气流场即能够充满整个蒸发塔;三喷嘴的雾化蒸发效果可以使蒸发塔出口温
脱硫废水旁路塔雾化蒸发数值模拟.doc
脱硫废水旁路塔雾化蒸发数值模拟脱硫废水成分复杂难以回用一些电厂已开始采用烟道雾化蒸发处理技术对其进行处理。脱硫废水直接喷入烟道会带来腐蚀、积灰、堵塞等问题设置旁路蒸发塔对脱硫废水进行干燥是一种较好的选择。为研究此项技术以某330MW机组为例通过计算脱硫废水与烟气的热质平衡确定了烟气抽取量建立了物理模型利用数值模拟的方法对烟气流场进行优化对喷嘴布置方式、液滴直径、烟气温度等的选择进行稳态模拟。结果表明:抽取烟气量仅占总烟气量的2.27%烟气流场即能够充满整个蒸发塔;三喷嘴的雾化蒸发效果可以使蒸发塔出口温度达
脱硫废水旁路塔雾化蒸发数值模拟.doc
脱硫废水旁路塔雾化蒸发数值模拟脱硫废水成分复杂难以回用,一些电厂已开始采用烟道雾化蒸发处理技术对其进行处理。脱硫废水直接喷入烟道会带来腐蚀、积灰、堵塞等问题,设置旁路蒸发塔对脱硫废水进行干燥是一种较好的选择。为研究此项技术,以某330MW机组为例,通过计算脱硫废水与烟气的热质平衡,确定了烟气抽取量,建立了物理模型,利用数值模拟的方法对烟气流场进行优化,对喷嘴布置方式、液滴直径、烟气温度等的选择进行稳态模拟。结果表明:抽取烟气量仅占总烟气量的2.27%,烟气流场即能够充满整个
350MW机组脱硫废水旁路烟道蒸发改造数值模拟分析.pptx
350MW机组脱硫废水旁路烟道蒸发改造数值模拟分析目录项目背景和意义脱硫废水处理的重要性旁路烟道蒸发技术的原理和应用数值模拟在改造设计中的作用改造方案设计旁路烟道蒸发系统设计改造后系统性能预测改造方案的优势和局限性数值模拟方法和模型建立流体动力学模拟方法数学模型的建立和简化边界条件和初始条件的设定模拟结果分析和讨论流场和温度场的分布改造前后性能对比分析对环境的影响评估结论和建议改造方案的有效性和可行性对其他机组的适用性和推广价值对未来研究的展望THANKYOU
脱硫废水旋转喷雾蒸发与旁路烟道蒸发特性研究.docx
脱硫废水旋转喷雾蒸发与旁路烟道蒸发特性研究标题:脱硫废水旋转喷雾蒸发与旁路烟道蒸发特性研究摘要:脱硫废水是燃煤发电厂中产生的一种主要废水,其中包含大量的二氧化硫和悬浮颗粒物。为了解决脱硫废水处理的问题,本研究以旋转喷雾蒸发和旁路烟道蒸发为研究对象,探讨了两种方法在脱硫废水处理中的特性。通过实验和数值模拟,对两种方法的蒸发效果、能耗、排放物控制等关键指标进行了系统性研究分析。研究结果表明,旋转喷雾蒸发和旁路烟道蒸发两种方法在脱硫废水处理中具有一定的优势和适用性,可以为相关工程的设计和优化提供参考。关键词:脱