
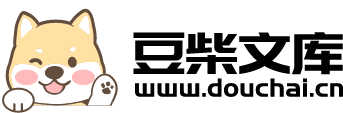
球头销冷镦工艺.doc
依波****bc
在线预览结束,喜欢就下载吧,查找使用更方便
相关资料
球头销冷镦工艺.doc
汽车球头销冷挤压工艺分析与模具设计关键字:球头销|镦挤|模具设计|组合凹模|有限元模拟摘要:球头销是汽车上的重要连接零件,要求结构强度高,宜采用冷精锻成形。采用镦挤加工方法,分析了某汽车球头销的成形工艺,对金属的塑性变形进行了合理分配,完成了加工此零件所需的三个道次工艺设计。同时,为验证设计工艺的合理性,采用有限元模拟手段,对该球头销的镦挤成形过程进行仿真,得到了金属流动的位移场、速度场及应力—应变场。模拟结果表明,设计的三道次镦挤工艺方案能够保证球头销的顺利成形。1概述球头销是汽车、拖拉机上的重要连接零
球头销冷镦工艺.doc
汽车球头销冷挤压工艺分析与模具设计关键字:球头销|镦挤|模具设计|组合凹模|有限元模拟摘要:球头销是汽车上的重要连接零件,要求结构强度高,宜采用冷精锻成形。采用镦挤加工方法,分析了某汽车球头销的成形工艺,对金属的塑性变形进行了合理分配,完成了加工此零件所需的三个道次工艺设计。同时,为验证设计工艺的合理性,采用有限元模拟手段,对该球头销的镦挤成形过程进行仿真,得到了金属流动的位移场、速度场及应力—应变场。模拟结果表明,设计的三道次镦挤工艺方案能够保证球头销的顺利成形。1概述球头销是汽车、拖拉机上的重要连接零
球头销冷镦工艺.docx
汽车球头销冷挤压工艺分析与模具设计关键字:球头销|镦挤|模具设计|组合凹模|有限元模拟摘要:球头销是汽车上的重要连接零件,要求结构强度高,宜采用冷精锻成形。采用镦挤加工方法,分析了某汽车球头销的成形工艺,对金属的塑性变形进行了合理分配,完成了加工此零件所需的三个道次工艺设计。同时,为验证设计工艺的合理性,采用有限元模拟手段,对该球头销的镦挤成形过程进行仿真,得到了金属流动的位移场、速度场及应力—应变场。模拟结果表明,设计的三道次镦挤工艺方案能够保证球头销的顺利成形。1概述球头销是汽车、拖拉机上的重要连接零
球头销冷镦成形工艺的逃逸粒子群优化算法.docx
球头销冷镦成形工艺的逃逸粒子群优化算法标题:球头销冷镦成形工艺的逃逸粒子群优化算法摘要:随着工业的发展和要求的提高,制造业对高质量和高效率的生产过程需求日益增加。其中,球头销冷镦成形工艺在汽车、机械等领域中应用广泛。然而,传统的球头销冷镦成形工艺存在一些问题,如加工精度低、能耗高等。为了解决这些问题,本文提出了一种基于逃逸粒子群优化算法的球头销冷镦成形工艺优化方法。通过对逃逸粒子群算法的介绍和原理分析,本文将该算法应用于球头销冷镦成形工艺参数优化中。实验结果表明,该方法能够有效提高球头销冷镦成形工艺的加工
球头销多工位冷锻工艺.docx
球头销多工位冷锻工艺球头销多工位冷锻工艺摘要:球头销多工位冷锻工艺是一种高效、精确的金属成形工艺,广泛应用于汽车、航空航天等行业的零部件制造中。本文将从工艺原理、工艺参数的选择以及工艺优势等方面对球头销多工位冷锻工艺进行探讨,以期为相关领域的研究提供参考。1.引言球头销多工位冷锻工艺是一种通过金属材料在冷态下经一系列工位的变形,实现产品制造的高效、精确的成形工艺。它具有成形速度快、成形精度高等优点,在汽车、航空航天等领域广泛应用于零部件的制造。2.工艺原理球头销多工位冷锻工艺的基本原理是通过在工位上施加压