
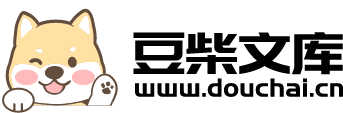
TPM设备预防保养.docx
又珊****ck
亲,该文档总共17页,到这已经超出免费预览范围,如果喜欢就直接下载吧~
相关资料
TPM设备预防保养.docx
编号:时间:2021年x月x日书山有路勤为径,学海无涯苦作舟页码:第页共NUMPAGES17页第PAGE\*MERGEFORMAT17页共NUMPAGES\*MERGEFORMAT17页設備預防保養與管理目錄TPM基本概念設備效率化改善之想法與進行方法零故障之想法與進行方法建立自主保養體制計劃保養與實施第一章:TPM基本概念TPM的定義1971年的定義:TPM:TotalProductiveMaintenance全面生產設備保養以達成設備的最高效率為目標建立以保養預防,預防保養,改良保養
TPM设备预防保养.docx
编号:时间:2021年x月x日书山有路勤为径学海无涯苦作舟页码:設備預防保養與管理目錄TPM基本概念設備效率化改善之想法與進行方法零故障之想法與進行方法建立自主保養體制計劃保養與實施第一章:TPM基本概念TPM的定義1971年的定義:TPM:TotalProductiveMaintenance全面生產設備保養以達成設備的最高效率為目標建立以保養預防預防保養改良保養之設備生涯為對象的全面性生產保養製度規劃設備的人(計劃部門)使用者(製造
TPM设备预防保养.docx
编号:时间:2021年x月x日书山有路勤为径,学海无涯苦作舟页码:第页共NUMPAGES17页第PAGE\*MERGEFORMAT17页共NUMPAGES\*MERGEFORMAT17页設備預防保養與管理目錄TPM基本概念設備效率化改善之想法與進行方法零故障之想法與進行方法建立自主保養體制計劃保養與實施第一章:TPM基本概念TPM的定義1971年的定義:TPM:TotalProductiveMaintenance全面生產設備保養以達成設備的最高效率為目標建立以保養預防,
TPM设备预防保养.docx
编号:时间:2021年x月x日书山有路勤为径,学海无涯苦作舟页码:第页共NUMPAGES17页第PAGE\*MERGEFORMAT17页共NUMPAGES\*MERGEFORMAT17页設備預防保養與管理目錄TPM基本概念設備效率化改善之想法與進行方法零故障之想法與進行方法建立自主保養體制計劃保養與實施第一章:TPM基本概念TPM的定義1971年的定義:TPM:TotalProductiveMaintenance全面生產設備保養以達成設備的最高效率為目標建立以保養預防,
TPM设备预防保养.docx
编号:时间:2021年x月x日书山有路勤为径学海无涯苦作舟页码:設備預防保養與管理目錄TPM基本概念設備效率化改善之想法與進行方法零故障之想法與進行方法建立自主保養體制計劃保養與實施第一章:TPM基本概念TPM的定義1971年的定義:TPM:TotalProductiveMaintenance全面生產設備保養以達成設備的最高效率為目標建立以保養預防預防保養改良保養之設備生涯為對象的全面性生產保養製度規劃設備的人(計劃部門)使用者(製造