
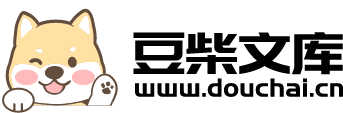
五胀形与翻边.pptx
胜利****实阿
亲,该文档总共103页,到这已经超出免费预览范围,如果喜欢就直接下载吧~
相关资料
五胀形与翻边.pptx
§5.1胀形软模胀形法液压胀形法起伏成形自行车多通接头/进入90年代,由于燃料和原材料成本的原因及环保法规对废气排放的严格限制,使汽车结构的轻量化显得日益重要。除了采用轻体材料如铝合金和镁合金等,减轻重量的另一个重要的途径就是在结构上采用以空代实和变截面等结构件,即对于承受以弯曲或扭转载荷为主的构件,采用空心结构既可以减轻重量、节约材料,又可以充分利用材料的强度和刚度。管件的液压柔性成形正是在这样的背景下开发出来的一种制造空心轻体构件的先进制造技术。此项技术在德国、美国等发达国家已得到广泛的研究和应用。尤
第5章胀形与翻边.ppt
第5章胀形与翻边5.1胀形利用胀形模具,使板平面或圆柱面内局部区域坯料在双向拉应力作用下,产生两向伸长变形,厚度减薄,表面积增大,以获得所需要几何形状和尺寸制件的冲压工序。生产中起伏成形、圆柱形空心毛坯的鼓肚成形,波纹管及平板毛坯张拉成形均属胀形成形。胀形常与其它方式的成形同时发生。某些汽车、拖拉机覆盖件和一些复杂形状零件成形,常常包含一定程度胀形成分。胀形加工中,金属流动量小,因此,使坯料变形均匀以及控制整个成形工序中胀形变形量是决定成败及制件质量的关键。a)弯曲、局部胀形b)胀形扩展至变形结束图5-1
钣金与成型胀形与翻边.pptx
会计学利用模具强迫板料厚度减薄和表面积增大,以获得零件几何形状的冲压加工方法叫胀形。胀形方法:刚模胀形橡皮胀形液压胀形……胀形包括:起伏成形圆柱形空心毛坯胀形平板张拉成形……利用模具把板料上的孔缘或外缘翻成竖边的冲压加工方法叫翻边。按工艺特点,翻边分为:内孔(圆孔或非圆孔)翻边外缘翻边(内曲翻边、外曲翻边)变薄翻边……按变形性质,翻边分为:伸长类翻边压缩类翻边变薄翻边(属体积成形)伸长类翻边的特点:变形区材料切向受拉应力,切向产生伸长变形,导致厚度减薄,容易发生破裂,如圆孔翻边、外缘的内曲翻边等。压缩类翻
一种翻边胀锥动力装置.pdf
本发明涉及一种翻边胀锥动力装置,包括箱体、动力电机、翻边动力组件和胀锥动力组件;所述动力电机固定在所述箱体上,所述箱体上枢接有一动力轴,所述动力电机的输出端与所述动力轴传动连接;所述翻边动力组件包括翻边凸轮、翻边杠杆和翻边拉杆,所述翻边凸轮固定在所述动力轴上,所述翻边杠杆的中部枢接于所述箱体上且其两端分别与所述翻边凸轮和翻边拉杆连接;所述胀锥动力组件包括胀锥凸轮、胀锥杠杆和胀锥拉杆,所述胀锥凸轮固定在所述动力轴上,所述胀锥杠杆枢接于所述箱体上且其两端分别与所述胀锥凸轮和胀锥拉杆连接。本发明的翻边胀锥动力装
翻边装置及翻边机.pdf
本发明提供了一种翻边装置及翻边机,涉及材料成型设备的技术领域,包括油缸、油缸杆、滑动装置、第一限位装置、弹簧、固定座、压紧轮和成型轮;滑动装置包括第一滑动装置和第二滑动装置,通过油缸对于滑动装置施加作用力,从而使得滑动装置移动,解决了现有技术中存在的结构复杂笨重,成型尺寸不稳定,生产效率以及生产质量低下的技术问题,实现了桶状材料的逐步成型,更加实用,适于推广适使用;本发明提供的翻边机,包括送料装置、旋转装置和翻边装置;通过翻边装置设置为两个用于将旋转装置上的桶状材料的双侧同时翻边,解决了现有技术中存在的单