
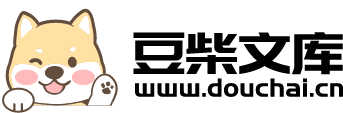
车床主轴加工工艺.ppt
梅雪****67
亲,该文档总共55页,到这已经超出免费预览范围,如果喜欢就直接下载吧~
相关资料
车床主轴加工工艺.doc
机械制造工艺学课程设计——CA6140机床主轴加工工艺设计班级:组员:指导教师:一、零件的结构特点及设计要求5二、CA6140车床主轴技术要求及功用6三、零件毛坯的选择及热处理7四、基准的选择8五、工序加工中的主要问题9六、加工阶段的划分11七、加工工序的安排和工序的确定11八、工序具体内容的确定15九、计算切削速度16⒈对小端端面有16⒉则对大端面同理有17⒊.钻中心孔17⒋:粗车外圆17⒌:车大端各部(大端外圆、短锥、端面、台阶)20⒍:仿
车床主轴加工工艺.ppt
车床主轴的功用和结构特点及设计要求车床主轴的结构特点既是阶梯轴又是空心轴;是长径比小于12的刚性轴不但传递旋转运动和扭矩而且是工件或刀具回转精度的基础主要加工表面有内外圆柱面、圆锥面次要表面有螺纹、花键、沟槽、端面结合孔等机械加工工艺主要是车削、磨削其次是铣削和钻削特别值得注意的工艺问题有:1)定位基准的选择;2)加工顺序的安排;3)深孔加工;4)热处理变形。车床主轴的功用承受扭转力矩;承受弯曲力矩;保证回转运动精度。车床主轴的设计要求扭转和弯曲刚度高;回转精度高(径向圆跳动、端面圆跳动、回转轴
车床主轴加工工艺.doc
机械制造工艺学课程设计——CA6140机床主轴加工工艺设计班级:组员:指导教师:TOC\o"1-3"\h\uHYPERLINK\l_Toc1010一、零件的结构特点及设计要求PAGEREF_Toc10105HYPERLINK\l_Toc28413二、CA6140车床主轴技术要求及功用PAGEREF_Toc284136HYPERLINK\l_Toc29303三、零件毛坯的选择及热处理PAGEREF_Toc293037HYPERLINK\l_Toc16619四、基准
车床主轴加工工艺.docx
编号:时间:2021年x月x日书山有路勤为径,学海无涯苦作舟页码:第页共NUMPAGES42页第PAGE\*MERGEFORMAT42页共NUMPAGES\*MERGEFORMAT42页机械制造工艺学课程设计——CA6140机床主轴加工工艺设计班级:组员:指导教师:TOC\o"1-3"\h\uHYPERLINK\l_Toc1010一、零件的结构特点及设计要求PAGEREF_Toc10105HYPERLINK\l_Toc28413二、CA6140车床主
车床主轴加工工艺.docx
编号:时间:2021年x月x日书山有路勤为径,学海无涯苦作舟页码:第页共NUMPAGES42页第PAGE\*MERGEFORMAT42页共NUMPAGES\*MERGEFORMAT42页机械制造工艺学课程设计——CA6140机床主轴加工工艺设计班级:组员:指导教师:TOC\o"1-3"\h\uHYPERLINK\l_Toc1010一、零件的结构特点及设计要求PAGEREF_Toc10105HYPERLINK\l_Toc28413二、CA6140车床主