
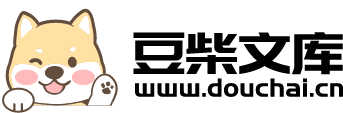
一种POY纺丝方法.pdf
含平****ng
在线预览结束,喜欢就下载吧,查找使用更方便
相关资料
一种POY纺丝方法.pdf
本发明提供一种POY的纺丝方法,该方法采用100/50目两层滤网卷在一起,卷至10层的多层滤网,过滤熔体中的杂质。过滤后的熔体由圆形喷丝板上的喷丝孔喷出形成多股单丝细流,所述喷丝板具有两圈呈同心圆排列分布的喷丝孔,两圈喷丝孔分别位于直径分别为30mm和66mm的同心圆处,喷丝孔为带锥孔的圆柱形孔。所述纺丝方法采用先进的环吹风冷却技术对喷丝孔喷出的多股单丝细流进行冷却。采用以上方法不仅能够延长清板周期、减少生产消耗,而且能够充分混匀熔体过滤杂质、减少单丝毛羽和断头,有效提高超细旦多孔纤维的条干均匀性,提升产
一种由FDY纺丝装置进行POY纺丝的方法和装置.pdf
本发明涉及一种FDY装置的改装生产POY的方法和装置。一种由FDY纺丝装置进行POY纺丝的方法,所述的FDY纺丝装置包括箱体、侧吹风窗、甬道、第一热辊、第二导丝辊和卷绕头,进行POY纺丝时,原FDY纺丝装置的油轮停用,在甬道的上方增设油嘴上油,并将第一热辊前预网络下导丝钩以及梳型分丝器通过设置加长杆外移,使纺丝中心线外移;同时,原FDY纺丝装置的第二热辊停用,保留第一热辊和第二导丝辊,丝束一次通过第一热辊,并在第二导丝辊绕4~5圈进一步外移纺丝中心线,丝束然后进入所述的卷绕头实现卷绕。本发明实现了在热辊式
一种POY化纤熔体纺丝设备及纺丝工艺.pdf
本发明公开了POY化纤熔体纺丝技术领域的一种POY化纤熔体纺丝设备及纺丝工艺,包括支架,所述支架固定连接有熔体挤压箱和水池,所述水池位于熔体挤压箱正下方,所述熔体挤压箱底壁固定连通有若干个等距分布的出丝管,所述出丝管与水池之间均设有循环水冷机构,所述循环水冷机构包括外包管,所述外包管固定套设于出丝管外侧,所述外包管外壁的上端固定连通有支管;本发明采用水冷的方式对丝体进行冷却,水冷的冷却效果大于传统风冷的冷却效果,加速了丝体冷却成形的时间,缩短了正在成型的丝体凌空的长度,从而降低了成型阶段丝体的抖动幅度,进
超细POY纺丝工艺探讨.docx
超细POY纺丝工艺探讨一、引言随着科技的不断进步,人们对生活品质的要求也越来越高。对于纺织行业,产品的质量、外观等方面的要求也越来越高。超细POY纺丝技术的出现,大大满足了市场上的需求。本文将探讨超细POY纺丝技术的原理、应用及发展。二、超细POY纺丝技术原理超细POY纺丝技术是通过控制熔体的流速、张力、气流等参数来实现的。首先,在强制熔融物料下,熔融物料流经一个壁孔,进入旋转圆锥状雾化器。在雾化器中,熔融物料经由离心力和空气反冲力,形成极细的螺旋状纤维。随后通过拉伸和丝轮的帮助,使纱线的拉伸倍数增加,从
黑色锦纶6POY纺丝工艺.docx
黑色锦纶6POY纺丝工艺黑色锦纶6POY的纺丝工艺摘要黑色锦纶6POY是一种纺丝工艺,广泛应用于纤维行业。本文通过对黑色锦纶6POY的生产过程、工艺参数和质量控制等方面的研究,探讨了黑色锦纶6POY的纺丝工艺。研究结果表明,优化工艺参数和加强质量控制可以提高黑色锦纶6POY的成品质量,提高生产效率。1.引言黑色锦纶6POY是一种合成纤维,具有优良的物理和化学性能,广泛应用于纤维制造业。黑色锦纶6POY的纺丝工艺对成品质量和生产效率具有重要影响。因此,深入研究黑色锦纶6POY的纺丝工艺对于提高产量和降低成本