
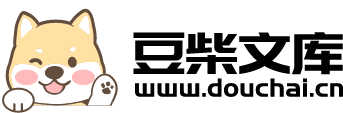
航空铝合金微弧氧化方法.pdf
书生****写意
在线预览结束,喜欢就下载吧,查找使用更方便
相关资料
航空铝合金微弧氧化方法.pdf
本发明通过提高成膜电解液成分并加大反应初期脉冲放电能量来改善成膜速度,将电压引入到高压放电区域,提高膜层厚度的同时保证膜层质量及成膜稳定性。本发明可以使2A14铝合金零件表面膜层厚度达到110微米以上,为机械加工留有充分磨削余量的同时保证了磨削后的光度及致密度要求,达到航空用零件粗糙度、硬度及厚度的使用要求。
铝合金微弧氧化工艺研究.pdf
武汉理工大学硕士学位论文铝合金微弧氧化工艺研究姓名:马晋申请学位级别:硕士专业:机械设计及理论指导教师:胡正前2003.5.1摘要弧氯化工艺生成的陶瓷氧化膜厚度可达20¨300铝及其余金在工业上的应用越来越广泛,但铝及其合金的表露磴度祗,辩|癌撰後戆差,辩鑫纯锈溶滚窝笼税酸簿溶液斡辩瘸蚀蚀差,制约了铝仑金的应用。可以通过表两涂装、热喷涂、气摺沉积、电镀、化学转化膜、电化学氧化等袭西处理方法对铝会金表面进行处理,褥高铝合龛表面性能,其中较常用的是电化学氧化方法中的阳极氯化工艺。阳极飘化工艺基本原理是,将铝或
铝合金微弧氧化工艺的研究.docx
铝合金微弧氧化工艺的研究随着现代工业技术的不断发展,铝合金在各个领域的应用越来越广泛,如航空、汽车、电子等领域。但是,铝合金表面的防腐、耐磨等性能还不够理想,因此需要对铝合金表面进行改进。微弧氧化工艺是一种有效的表面处理方法,可以提高铝合金表面的硬度、耐腐蚀性和耐磨性,为铝合金的应用提供了无限的可能。1.微弧氧化工艺的概述:微弧氧化工艺,又称为电解微弧氧化,是利用高压脉冲电进行氧化反应的表面处理技术。该工艺是在高压电场下,利用阳极溶液电解离产生的氧化物,在阳极材料表面上生成一层坚硬、致密、陶瓷状的氧化膜。
铝合金微弧氧化工艺研究.docx
铝合金微弧氧化工艺研究铝合金微弧氧化工艺研究摘要:本文介绍了铝合金微弧氧化的基本原理和工艺流程,并对当前研究的进展进行了综述。文章也提出了未来可能的研究方向,以期为铝合金微弧氧化工艺的改进和发展提供参考。关键词:铝合金、微弧氧化、电解液、遗传算法、表面处理1.引言铝合金是一种重要的结构材料,因其轻质、高强度、易加工等特点,广泛应用于汽车、航空、航天、建筑等领域。随着技术的发展,人们对铝合金的表面性能要求越来越高,表面处理技术也得到了广泛的关注。微弧氧化是一种能够在铝合金表面形成陶瓷膜的电化学处理技术,具有
一种微弧氧化铝合金的制备方法.pdf
本发明提供了一种微弧氧化铝合金的制备方法,通过在一次微弧氧化后进行抛光处理有效的平整待处理金属表面,保留微弧氧化层中的过渡层和部分致密层,并将其作为二次微弧氧化的基质,获得的微弧氧化膜表面形态主要为火山熔岩口的内凹形态,有效的避免了无定型或者杂孔表面形态,明显减少了表面多孔层的形成,获得的微弧氧化表面的硬度高,粗糙度Ra和摩擦系数μ低高品质涂层。