
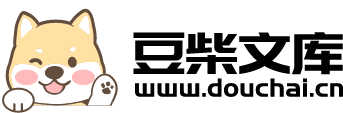
换热器管板与换热管内孔搭接焊接方法.pdf
元枫****文章
在线预览结束,喜欢就下载吧,查找使用更方便
相关资料
换热器管板与换热管内孔搭接焊接方法.pdf
换热器管板与换热管内孔搭接焊接方法,属于压力容器制造领域,克服了现有技术的难题。该方法是:首先按照换热管⑵的尺寸初次加工管板孔,然后对管孔进行二次扩孔,使管孔的尺寸比换热管外径大2‑3mm,同时保留管板下部2mm的凸台⑶;焊接时先采用手工钨极氩弧焊从管板侧伸入管孔内自熔点焊固定换热管⑵和管板⑴;将氩气背保护装置安装在需保护部位,将内孔搭接焊专用焊接枪头⑷从管板侧伸入管孔内,调整好钨极与待焊部位的距离;背保护装置⑸通入保护氩气,开机进行施焊;施焊完成后对焊接接头进行PT检测,有缺陷则修补。本发明可避免换热管
空冷换热器换热管-管板焊接方法及应用简介.docx
空冷换热器换热管-管板焊接方法及应用简介空冷换热器是一种常用的换热设备,用于进行热交换的同时实现冷却或加热的目的。换热管-管板焊接是空冷换热器中常用的连接方式之一,具有结构简单、换热效率高等优点,被广泛应用于各种工业领域。在空冷换热器中,换热管起到了传热介质的作用,而管板则起到支撑和密封的作用。换热管-管板焊接是将换热管与管板焊接在一起,实现二者之间的连接。根据不同的换热器结构和工艺要求,换热管-管板焊接有多种方法,包括对焊、套焊、头对头焊和封头焊接等。对焊是最常用的一种焊接方法,通常应用于小型空冷换热器
钛管换热器的换热管与管板焊接工艺介绍.docx
钛管换热器的换热管与管板焊接工艺介绍摘要:文章介绍了以海水作为冷却介质的换热器中一种以爆炸复合钛钢板作管板、以钛管作换热管的换热管与管板焊接的工艺评定及生产制作中的焊接工艺。文章为钛制换热器的生产制造提供可借鉴经验。关键词:钛管换热管;复合钛钢板管板;换热管与管板工艺评定;生产制作滨海电站的换热器设备若采用常规不锈钢管做换热管、低合金钢作管板管板和换热管会在一两年内发生严重的点腐蚀、溃蚀等现象使用周期短不但成本高而且有碍生产。我公司设计制造的以钛管作为换
板换换热器及换热原理.ppt
热交换器及换热原理如何进行热交换基础概念思考常用类型:整体结构整体结构及图工作示意图补充图示总结标识介绍整体结构整体结构工作原理补充说明图示持热管简介必要性及设计原理设计原理换热器面积的计算续计算热交换器面积的一般公式:续热交换器中逆流传热的温度分配公式解释单项分析单项分析单项分析特别介绍分析分析.污垢聚集的速度取决于很多因素续术语对比总结本次培训结束
卧式固定管板式换热器及换热方法.pdf
卧式固定管板式换热器及换热方法,当要求换热面积较大时,为了缩短换热器长度、节省占地面积,只有增大壳体直径,增加换热管数量,造成管内介质流速降低,换热效率降低。卧式固定管板式换热器,其组成包括:筒体(1),所述的筒体一端连接左管板(2),所述的筒体另一端连接右管板(3),所述的左管板连接管箱筒体(4),所述的管箱筒体连接左管箱封头(5),所述的右管板连接右管箱封头(6),所述的筒体下端连接疏水罐(7),所述的筒体内上部装有管系(8),所述的管系上部装有蒸汽防冲装置(9)和直管换热管(10),所述的左管箱壳体