
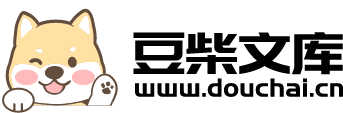
一种金属刻槽方法.pdf
梅雪****67
在线预览结束,喜欢就下载吧,查找使用更方便
相关资料
一种金属刻槽方法.pdf
本发明涉及一种金属刻槽方法,包括以下步骤:S1、使用光刻胶作为掩膜,利用刻蚀气体在金属表面刻蚀,形成槽;S2、利用氧化气体对槽壁和槽底的金属进行氧化,形成金属氧化物;S3、利用刻蚀气体对槽底的金属氧化物进行刻蚀,去除所述槽底的金属氧化物,保留槽壁的金属氧化物;S4、重复步骤S2和S3,直到刻槽深度达到要求为止。本发明通过循环次数来控制刻蚀深度,利用电感耦合等离子刻蚀机(ICP)刻蚀材料时是各向异性的特点,侧壁的刻蚀作用低于Bias方向。因此在刻蚀时,底部的金属氧化物被受到较强的轰击作用,很容易被刻蚀掉,而
一种金属盲槽的加工方法.pdf
本发明实施例公开了一种金属盲槽的加工方法,用于解决现有技术的加工方法只能将盲槽加工为内部全金属化或非金属化的技术问题。本发明实施例包括S1、通过加工设备在板件上加工出预设规格的盲槽;S2、对盲槽进行金属化处理,将盲槽的槽壁和槽底金属化;S3、对盲槽的槽壁和槽底进行电镀处理,在槽壁以及槽底的金属层表面镀上锡层;S4、用激光对盲槽的槽底金属层表面上的锡层进行烧蚀,去除锡层;S5、将经过烧蚀后的盲槽的槽底金属层表面进行碱性蚀刻,将金属层去除。本实施例中采用UV激光烧蚀掉锡层,露出槽底的铜层。再经过碱性蚀刻后,蚀
一种熔融金属槽侵蚀程度检测方法.pdf
本发明实施例提供一种熔融金属槽侵蚀程度检测方法,所述检测方法包括:将中上部固定有第一定位码和第二定位码的探棒的底端置于熔融金属槽底部,使所述第一定位码和第二定位码保持面向固定于固定位置的测距摄像头,来回多次滑动所述探棒,获得所述第一定位码和第二定位码分别相对于所述固定位置的向量数据;根据所述第一定位码和第二定位码分别相对于所述固定位置的向量数据、第一定位码和第二定位码之间的距离以及第二定位码与探棒底端之间的距离,计算得出探棒底端相对于固定位置的向量数据,从而获得反映所述熔融金属槽侵蚀轮廓的探棒底端的运动轨
检查刻槽取样质量的方法.docx
检查刻槽取样质量的方法检查刻槽取样质量的方法引言:刻槽取样是一种常用的地质取样方法,广泛应用于矿产资源勘探、工程勘探和环境调查等领域。刻槽取样质量的好坏直接影响到后续的分析和判断,因此准确评估刻槽取样质量至关重要。本文将介绍几种常用的检查刻槽取样质量的方法。一、外观检查法外观检查法是最简单、直观的一种方法,通过检查刻槽取样的外观来评估取样质量。具体步骤如下:1.观察刻槽取样表面的光滑度,取样表面应平坦光滑,无大块状物质或明显的凹凸不平;2.检查取样表面的颜色和纹理,如发现颜色异常、多色或明显的纹理,可能存
一种复合式路面CRC层表面刻槽方法.pdf
本发明公开了一种复合式路面CRC层表面刻槽方法,其包括如下步骤:S1、确定复合式路面结构设计参数;S2、根据步骤S1的复合式路面结构设计参数建立复合式路面有限元模型;S3、进行复合式路面有限元模型校准;S4、利用校准后的复合式路面有限元模型数据计算复合式路面层间抗剪等效剪切角度;S5、根据步骤S4的复合式路面层间抗剪等效剪切角度得到复合式路面CRC层表面刻槽面角度,从而确定复合式路面CRC层表面刻槽。本发明能设计一种产生较少水泥混凝土废渣,适用于复合式路面CRC层的表面刻槽。