
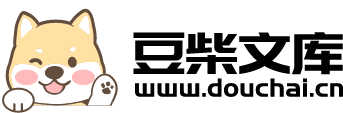
散斑干涉条纹测量系统设计.docx
文宣****66
在线预览结束,喜欢就下载吧,查找使用更方便
相关资料
散斑干涉条纹测量系统设计.docx
散斑干涉条纹测量系统设计摘要:为了测量散斑干涉条纹从而计算出被测物体的微位移提出了一种基于AT89S52芯片的解决方案。运用单片机驱动步进电机精准控制光敏传感器的移动利用传感器判定暗条纹中心结合软件进行实时处理获得再现干涉条纹间距。实验结果表明该设计方案对散斑位移的测量精度可达0.001mm。关键词:微位移测量;相干光学;单片微型计算机;步进电机;光敏传感器引言传统的散斑照相法通过摄取双曝光散斑图然后再现散斑图像即杨氏条纹并测量条纹间距再利用
散斑干涉条纹测量系统设计.docx
散斑干涉条纹测量系统设计摘要:为了测量散斑干涉条纹从而计算出被测物体的微位移提出了一种基于AT89S52芯片的解决方案。运用单片机驱动步进电机精准控制光敏传感器的移动利用传感器判定暗条纹中心结合软件进行实时处理获得再现干涉条纹间距。实验结果表明该设计方案对散斑位移的测量精度可达0.001mm。关键词:微位移测量;相干光学;单片微型计算机;步进电机;光敏传感器引言传统的散斑照相法通过摄取双曝光散斑图然后再现散斑图像即杨氏条纹并测量条纹间距再利用
散斑干涉与剪切散斑干涉的测量系统及测量方法.pdf
本发明提供一种散斑干涉与剪切散斑干涉的测量系统及测量方法,涉及光学测试技术领域。其特征在于:包括激光器和分束镜,所述激光器发射的激光经所述分束镜分为透射光和反射光;所述透射光经扩束镜扩束后照射至被测物形成漫反射光,所述反射光依次经光纤、透镜和分光棱镜后作为参考光进入光路;所述被测物表面的漫反射光依次经光阑、成像透镜和迈克尔逊剪切装置后,获得具有剪切量的两束物光;所述具有剪切量的两束物光和光纤引入的参考光在CCD相机的靶面上干涉,形成散斑干涉图。本发明可对被测物进行散斑和剪切的同步动态检测,是一种无损、全场
一种高精度散斑干涉相移条纹动态测量系统及方法.pdf
本发明为一种高精度散斑干涉相移条纹动态测量系统及方法,包括,激光器,用做光源,发出激光;压电陶瓷,可进行移动,且具有反射镜,反射镜用于反射激光并在物体表面产生相移散斑图;相机,用于捕捉图像;迈克尔逊干涉仪,用于产生干涉条纹;信号同步模块,用于制作同步信号发生电路;计算机,用于显示相机捕捉的图像,及计算干涉条纹图;其中,同步信号发生电路能够产生方波信号和阶梯信号,方波信号和阶梯信号的上升沿同步,方波信号用于控制相机的图像采集,阶梯信号用于控制压电陶瓷的移动产生相移图;阶梯波产生台阶电压,每个台阶的电压差值相
激光散斑的特性及其干涉条纹的滤波研究的综述报告.docx
激光散斑的特性及其干涉条纹的滤波研究的综述报告激光散斑是激光束通过不均匀介质时所产生的空间干涉现象。其特性使其在光学检测、高分辨率显微镜、数字全息术和波前相衬成像等应用中得到广泛应用。同时,散斑的干涉条纹也是研究光学干涉的重要工具。因此,综述激光散斑的特性及其干涉条纹的滤波研究显得尤为重要。激光散斑的特性主要包括其产生机理、散斑图案和相位噪声等方面。激光束产生散斑的根本原因是光的干涉作用。具体地说,当激光束通过介质时,它会和介质中的不均匀性相互作用,形成了一系列散斑图案。这些图案是由光子的相位差异所引起的