
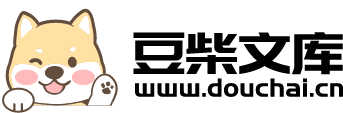
单晶叶片用氧化铝陶瓷型芯的发展概况.docx
努力****振宇
在线预览结束,喜欢就下载吧,查找使用更方便
相关资料
单晶叶片用氧化铝陶瓷型芯的发展概况.docx
单晶叶片用氧化铝陶瓷型芯的发展概况【摘要】本文综述了单晶叶片用氧化铝陶瓷型芯在国内外的发展概况较详细地介绍了单晶叶片用氧化铝陶瓷型芯的脱芯方法及国内外的部分研究成果据此提出了单晶叶片用氧化铝陶瓷型芯工程化应用研究的发展方向。1、概述单晶涡轮叶片是高性能航空发动机研制的重要关键部件使用性能要求高制造难度大被誉为“现代制造业皇冠上的明珠”。目前单晶叶片朝着单晶合金与高效冷却技术融合的方向发展因此单晶叶片具有薄壁空心、内腔结构复杂等结构特点要求陶瓷型芯应具有更好
单晶叶片用氧化铝陶瓷型芯的发展概况.docx
单晶叶片用氧化铝陶瓷型芯的发展概况【摘要】本文综述了单晶叶片用氧化铝陶瓷型芯在国内外的发展概况较详细地介绍了单晶叶片用氧化铝陶瓷型芯的脱芯方法及国内外的部分研究成果据此提出了单晶叶片用氧化铝陶瓷型芯工程化应用研究的发展方向。1、概述单晶涡轮叶片是高性能航空发动机研制的重要关键部件使用性能要求高制造难度大被誉为“现代制造业皇冠上的明珠”。目前单晶叶片朝着单晶合金与高效冷却技术融合的方向发展因此单晶叶片具有薄壁空心、内腔结构复杂等结构特点要求陶瓷型芯应具有更好
单晶叶片用氧化铝陶瓷型芯显气孔率研究.docx
单晶叶片用氧化铝陶瓷型芯显气孔率研究摘要:为了研究单晶叶片用氧化铝陶瓷型芯显气孔率的效果,本文从气孔率在单晶叶片加工过程中的作用、氧化铝陶瓷型芯的性能及其在制造单晶叶片中的应用等方面进行了探讨。研究表明,采用氧化铝陶瓷型芯可以显著提高单晶叶片的气孔率,从而改善其流体动力学性能,使其性能指标得到进一步提高。关键词:单晶叶片;氧化铝陶瓷型芯;气孔率;制造一、引言单晶叶片是高温燃气轮机中的主要叶片类型,其性能指标的提高对于提高燃气轮机热效率至关重要。在单晶叶片的制造过程中,气孔率一直是制约其性能指标提高的关键因
单晶铸造用陶瓷型芯.pdf
单晶铸造用陶瓷型芯,主要解决现有铸造陶瓷型芯的使用温度偏低的技术问题。它由下述原料按重量百分比组成,其中氧化钇60-90%,氧化铝1-20%,石蜡5-20%,蜂蜡0.25-0.5%,聚乙烯0.05-0.25%,油酸0.1-1%,硬脂酸0.1-1%。本发明适合用注射成型工艺连续生产复杂形状的陶瓷型芯,制成的陶瓷型芯的工作温度最高可达1700℃,完全满足了单晶铸造对陶瓷型芯的使用要求,扩大了陶瓷型芯的使用范围。
一种单晶叶片用氧化铝陶瓷型壳的制备方法.pdf
一种单晶叶片用氧化铝陶瓷型壳的制备方法,使用硅酸乙酯料浆制作具有层状结构层数至少为5层的型壳;1)型壳的第1层使用下列两种方案之一获得的硅酸乙酯料浆:方案1:将粒度1000-230#的电熔刚玉微细粉加入硅酸乙酯中;粘度按流杯粘度计Φ4,流净时间为57~62秒;方案2:将粒度要求200-325#的ZrSO4粉末加入硅酸乙酯中;粘度按流杯粘度计Φ4,流净时间为65~70秒;2)型壳的第1层之外的其余各层的硅酸乙酯料浆满足上述方案一的配方和配置顺序要求,搅拌后获得混合物的粘度按流杯粘度计Φ4,流净时间为30~3