
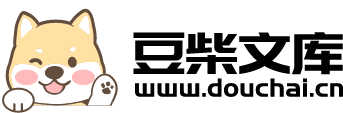
冷冲模具开裂原因分析.docx
雨巷****怡轩
在线预览结束,喜欢就下载吧,查找使用更方便
相关资料
冷冲模具开裂原因分析.docx
冷冲模具开裂原因分析摘要:通过物理光电学高倍精密仪器、构成Cr12模具钢的化学成分检测分析以及测试硬度等检验手段发现该种模具发生开裂主要在电火花线切割过程中产生的其主要表现为:脆性开裂。本文针对以上问题进行了简要的分析讨论希望对此种模具的生产能够提供有价值的参考资料以备在日后的加工生产中得以运用。关键词:Cr12模具钢;碳化物;脆性开裂中图分类号:TG162.41文献标识码:ACr12钢在合金钢的种类中属于碳含量与铬含量百分比较高的、被应用于
冷冲模具开裂原因分析.docx
冷冲模具开裂原因分析冷冲模具开裂原因分析摘要:冷冲模具开裂是模具制造和使用过程中常见的故障之一,对模具的正常使用和寿命造成了很大的影响。本文通过对冷冲模具开裂的原因进行分析,包括材料问题、设计问题、制造问题和使用问题等方面的因素,并提出了相应的解决方法,以期能够帮助模具制造和使用者更好地了解和解决冷冲模具开裂问题。关键词:冷冲模具;开裂原因;材料问题;设计问题;制造问题;使用问题1.引言冷冲模具在工业生产中起到至关重要的作用,广泛应用于各个行业,如汽车制造、电子设备、家电制造等。而冷冲模具开裂则是模具制造
冷冲模具开裂原因分析.docx
冷冲模具开裂原因分析摘要:通过物理光电学高倍精密仪器、构成Cr12模具钢的化学成分检测分析以及测试硬度等检验手段发现该种模具发生开裂主要在电火花线切割过程中产生的其主要表现为:脆性开裂。本文针对以上问题进行了简要的分析讨论希望对此种模具的生产能够提供有价值的参考资料以备在日后的加工生产中得以运用。关键词:Cr12模具钢;碳化物;脆性开裂中图分类号:TG162.41文献标识码:ACr12钢在合金钢的种类中属于碳含量与铬含量百分比较高的、被应用于
冷冲模具开裂原因分析.docx
冷冲模具开裂原因分析摘要:通过物理光电学高倍精密仪器、构成Cr12模具钢的化学成分检测分析以及测试硬度等检验手段发现该种模具发生开裂主要在电火花线切割过程中产生的其主要表现为:脆性开裂。本文针对以上问题进行了简要的分析讨论希望对此种模具的生产能够提供有价值的参考资料以备在日后的加工生产中得以运用。关键词:Cr12模具钢;碳化物;脆性开裂中图分类号:TG162.41文献标识码:ACr12钢在合金钢的种类中属于碳含量与铬含量百分比较高的、被应用于
阀体开裂原因分析.docx
阀体开裂原因分析阀体是阀门的主要组成部分,其质量和性能直接影响着阀门的使用寿命和安全性。然而,阀体开裂是阀门制造和使用过程中常见的问题之一,其原因包括材料缺陷、制造工艺不当、设计缺陷及使用条件不合理等多方面因素。本文将从以上几个方面对阀体开裂的原因进行分析。一、材料缺陷阀门的阀体通常采用铸铁、铸钢、锻钢等材料。这些材料往往存在着各种各样的缺陷,如气孔、疏松、夹杂、针孔等。这些缺陷虽然在肉眼下看不到,但在使用中可能会因受到冲击、振动、温度变化等因素的作用而导致阀体开裂。二、制造工艺不当阀体的制造过程中,如果