
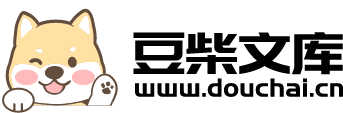
热水解工艺气对污泥厌氧消化运行的影响.docx
Ch****49
在线预览结束,喜欢就下载吧,查找使用更方便
相关资料
热水解工艺气对污泥厌氧消化运行的影响.docx
热水解工艺气对污泥厌氧消化运转的影响热水解作为高级厌氧消化的预处理工序其排放的废气——工艺气一般进入厌氧消化池进行处理。通过高安屯污泥处理中心项目运转实例分析通入热水解工艺气的消化池与未通入热水解工艺气的消化池在有机物分解率、沼气成分、污泥理化指标、沼气产率等方面的差异总结热水解工艺气对于厌氧消化运转的影响。针对生产运转实际提出对于工艺气处理的相关建议。01热水解工艺气的来源高安屯项目中采用蒸汽作为热源提供热水解反应所需温度。蒸汽由蒸汽锅炉提供蒸汽锅炉的燃料来自厌氧消化所产生的沼气。在热水解过程当中多余
详细运行数据对比污泥热水解厌氧消化与常规厌氧消化.doc
(完整word版)详细运行数据对比污泥热水解厌氧消化与常规厌氧消化(完整word版)详细运行数据对比污泥热水解厌氧消化与常规厌氧消化鸿淳环保,一站式为您解决污水处理难题www.hcpet.net(完整word版)详细运行数据对比污泥热水解厌氧消化与常规厌氧消化详细运行数据对比污泥热水解厌氧消化与常规厌氧消化热水解厌氧消化是近年来污泥处理的一个新的发展方向。选取小红门污泥处理中心工程运行数据,比较了热水解厌氧消化与常规厌氧消化的操作操作、泥质土壤、消化效果、气体产生量、沼气组成等;以及辅助系统。分析了工程运
详细运行数据对比污泥热水解厌氧消化与常规厌氧消化.doc
(完整word版)详细运行数据对比污泥热水解厌氧消化与常规厌氧消化(完整word版)详细运行数据对比污泥热水解厌氧消化与常规厌氧消化鸿淳环保,一站式为您解决污水处理难题www.hcpet.net(完整word版)详细运行数据对比污泥热水解厌氧消化与常规厌氧消化详细运行数据对比污泥热水解厌氧消化与常规厌氧消化热水解厌氧消化是近年来污泥处理的一个新的发展方向。选取小红门污泥处理中心工程运行数据,比较了热水解厌氧消化与常规厌氧消化的操作操作、泥质土壤、消化效果、气体产生量、沼气组成等;以及辅助系统。分析了工程运
污泥厌氧消化沼气安全系统的工艺设计.docx
污泥厌氧消化沼气安全系统的工艺设计摘要:本文以典型的污泥厌氧消化沼气安全利用系统为例着重从系统角度介绍了流程的设计、安全装置的设置以及系统压力的设定和控制。关键词:沼气利用安全系统工艺设计污泥厌氧消化是一种使污泥达到稳定状态的非常有效的处理方法。污泥中的有机物在厌氧条件下在产酸细菌和甲烷细菌的先后作用下经酸性消化阶段和碱性消化阶段分解为甲烷和二氧化碳为主要产物的消化气(沼气)。大中型污水处理厂对消化产生的沼气进行回收利用可以达到节约能源、降低运行成本的
污泥厌氧消化沼气安全系统的工艺设计.doc
污泥厌氧消化沼气安全系统的工艺设计论文名称:污泥厌氧消化沼气安全系统的工艺设计作者:史骏张韵杭世珺摘要:本文以典型的污泥厌氧消化沼气安全利用系统为例,着重从系统角度介绍了流程的设计、安全装置的设置以及系统压力的设定和控制。关键字:沼气利用安全系统工艺设计污泥厌氧消化是一种使污泥达到稳定状态的非常有效的处理方法。污泥中的有机物在厌氧条件下,在产酸细菌和甲烷细菌的先后作用下,经酸性消化阶段和碱性消化阶段分解为甲烷和二氧化碳为主要产物的消化气(沼气)。大中型污水处理厂对消化产生的沼气进行回收利用,可以达到节约能