
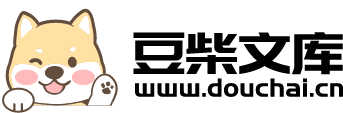
产品制造过程质量控制要点概述.ppt
YY****。。
亲,该文档总共54页,到这已经超出免费预览范围,如果喜欢就直接下载吧~
相关资料
产品制造过程质量控制要点概述.ppt
产品制造过程质量控制要点概述样件生产一、术语品质改善初物?初期流动管理?初物第1种情况:供应商必须进行产品的过程变更或设计变更申请,提交产品批准部门(设计变更为技术部,过程变更为进货检验部门)批准●新产品设计●新产品设计开发时就应编制品质保证计划,详见新产品开发品质保证展开计划()●技术质量交流(需形成交流备忘录)►研究图纸时发现的问题►零件的功能及特性(图纸上规定的要求、与其它零件的关联等)►制造上的问题点(精度、制造方法等)►生产设备、检测设备配置►工程管理标准(控制项目、管理要点)►产品检验标准(控
产品制造过程质量控制要点.ppt
产品制造过程质量控制要点样件生产一、术语品质改善初物?初期流动管理?初物第1种情况:供应商必须进行产品的过程变更或设计变更申请,提交产品批准部门(设计变更为技术部,过程变更为进货检验部门)批准●新产品设计●新产品设计开发时就应编制品质保证计划,详见新产品开发品质保证展开计划()●技术质量交流(需形成交流备忘录)►研究图纸时发现的问题►零件的功能及特性(图纸上规定的要求、与其它零件的关联等)►制造上的问题点(精度、制造方法等)►生产设备、检测设备配置►工程管理标准(控制项目、管理要点)►产品检验标准(控制项
产品制造过程质量控制要点.ppt
产品制造过程质量控制要点样件生产一、术语品质改善初物?初期流动管理?初物第1种情况:供应商必须进行产品的过程变更或设计变更申请,提交产品批准部门(设计变更为技术部,过程变更为进货检验部门)批准●新产品设计●新产品设计开发时就应编制品质保证计划,详见新产品开发品质保证展开计划()●技术质量交流(需形成交流备忘录)►研究图纸时发现的问题►零件的功能及特性(图纸上规定的要求、与其它零件的关联等)►制造上的问题点(精度、制造方法等)►生产设备、检测设备配置►工程管理标准(控制项目、管理要点)►产品检验标准(控制项
产品制造过程质量控制要点.ppt
产品制造过程质量控制要点样件生产一、术语品质改善初物?初期流动管理?初物第1种情况:供应商必须进行产品的过程变更或设计变更申请提交产品批准部门(设计变更为技术部过程变更为进货检验部门)批准●新产品设计●新产品设计开发时就应编制品质保证计划详见新产品开发品质保证展开计划()●技术质量交流(需形成交流备忘录)►研究图纸时发现的问题►零件的功能及特性(图纸上规定的要求、与其它零件的关联等)►制造上的问题点(精度、制造方法等)►
产品制造过程质量控制要点.ppt
产品制造过程质量控制要点样件生产一、术语品质改善初物?初期流动管理?初物第1种情况:供应商必须进行产品的过程变更或设计变更申请,提交产品批准部门(设计变更为技术部,过程变更为进货检验部门)批准●新产品设计●新产品设计开发时就应编制品质保证计划,详见新产品开发品质保证展开计划()●技术质量交流(需形成交流备忘录)►研究图纸时发现的问题►零件的功能及特性(图纸上规定的要求、与其它零件的关联等)►制造上的问题点(精度、制造方法等)►生产设备、检测设备配置►工程管理标准(控制项目、管理要点)►产品检验标准(控制项