
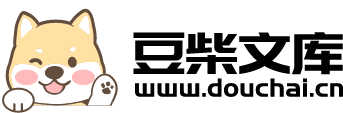
一种径向水平井钻井用自进式高压射流喷头.pdf
黛娥****ak
在线预览结束,喜欢就下载吧,查找使用更方便
相关资料
一种径向水平井钻井用自进式高压射流喷头.pdf
本发明涉及一种径向水平井钻井用自进式高压射流喷头,主要包括壳体、涡轮转子、耐磨钢球、挡板等。其技术特征是:壳体上加工有顶尖、前向喷嘴和后向喷嘴,并在壳体外表面敷焊硬质合金;壳体内部装有涡轮转子,涡轮转子上、下两端均加工有球形凹槽,通过上、下两个耐磨钢球定位;上耐磨钢球放置在壳体内部与涡轮转子的球形凹槽之间,下耐磨钢球放置在涡轮转子与挡板上的球形凹槽之间;壳体与挡板通过螺纹连接在一起,挡板上均匀分布4~6个注水孔。本发明结构简单,工作可靠,可广泛应用于径向水平井钻井作业中。
一种径向水平井用自进式喷射钻头.pdf
本发明涉及一种径向水平井用自进式喷射钻头,主要包括钻头、旋转轴、壳体、涡轮定子、涡轮转子、后部短节、扶正器和后接管,壳体内部装有涡轮系统,壳体置于钻头与扶正器中间,前部通过旋转轴与钻头相连,后部通过后接管与扶正器相连,涡轮转子通过转子螺母和平键键固紧在旋转轴上,旋转轴后部通过滑动轴承套与后部短节相连,扶正器与后接管空套。涡轮系统通过平键传递扭矩给旋转轴,旋转轴带动钻头旋转,形成钻头旋转喷射钻井,提高破岩能力和钻井效率,旋转的钻头起到修饰井壁的作用;通过涡轮系统的流体从壳体上后喷孔喷出产生自进力,推动喷射钻
一种自进式高压水射流钻头.pdf
本发明公开了一种自进式高压水射流钻头,主要包括钻头本体、涡轮转子、上耐磨钢球、下耐磨钢球、挡板,其特征在于,中心设盲空心轴作为支承,盲空心轴上有环形出水孔,盲空心轴前端连接在钻头本体的前端,钻头本体上设置前向喷嘴和后向喷嘴;盲空心轴的左右两侧对称装有涡轮转子,涡轮转子上、下两端均加工有球形凹槽,通过上、下两个耐磨钢球定位,上耐磨钢球放置在钻头本体与涡轮转子的球形凹槽之间,下耐磨钢球放置在涡轮转子与挡板上的球形凹槽之间,钻头本体与其内部的挡板通过螺纹连接在一起。本发明能实现各种岩矿层的快速连续钻长孔,结构简
基于Fluent自进式旋转射流喷头的数值模拟.docx
基于Fluent自进式旋转射流喷头的数值模拟摘要本文基于Fluent自进式旋转射流喷头的数值模拟,对旋转射流的流场特性及其对多相反应的影响进行研究。研究结果表明,旋转射流能够增强混合和传质,从而提高反应效率。同时,为了优化喷头结构,我们建立了喷头的几何模型,并通过数值模拟分析了喷头的性能参数。最后,我们探讨了该喷头在工业生产中的应用前景并展望了未来研究的方向。关键词:Fluent;自进式旋转射流;喷头;多相反应;流场特性;数值模拟AbstractThispaperstudiestheflowcharact
基于水射流的自进式喷头设计及试验探究的开题报告.docx
基于水射流的自进式喷头设计及试验探究的开题报告摘要本文介绍了一个基于水射流的自进式喷头的设计和试验探究。本文首先介绍了水射流技术的基本理论和应用领域。随后,文章详细介绍了自进式喷头的工作原理和设计流程。设计过程中,选择了合适的材料,并结合计算机模拟进行了实验验证,最终得到了满足要求的自进式喷头。本文还对自进式喷头的性能进行了测试,结果表明自进式喷头的稳定性、均匀性和效率均优于传统喷头。最后,文章总结了设计和试验的结果,以及未来工作的展望。关键词:水射流技术;自进式喷头;工作原理;设计流程;实验验证前言水射