
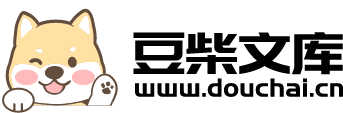
陶瓷研磨体应用条件.pptx
YY****。。
亲,该文档总共25页,到这已经超出免费预览范围,如果喜欢就直接下载吧~
相关资料
陶瓷研磨体应用条件.pptx
经过一年多的应用实践,陶瓷研磨体在国内几十家水泥企业已被接受和认可。该项技术的节能降耗效果,在当前水泥产能过剩、市场竞争的形势下,得到了越来越多的水泥科技工作者的青睐。但是,我们还必须清醒地看到,不是所有的水泥粉磨系统都能够应用陶瓷研磨体,就我国目前3000多台水泥球磨机现状来看,可分为以下三种情况:1.工艺设备条件较适宜,可以直接在尾仓用陶瓷研磨体替代钢球或钢锻;2.必须经过必要的设备技术改造,才能用陶瓷研磨体替代钢球或钢锻;3.由于入磨物料粒度≥5mm等原因,目前还不能用陶瓷研磨体替代钢球或钢锻。球磨
纳米陶瓷研磨体的特性与应用研究.docx
纳米陶瓷研磨体的特性与应用研究纳米陶瓷研磨体是一种具有特殊性能和广泛应用前景的新型磨料材料。它由纳米级颗粒组成,具有很小的颗粒尺寸、高度均匀的分布和良好的分散性。在磨削和抛光等工艺中,纳米陶瓷研磨体表现出独特的磨削性能和优异的表面质量,因此引起了广泛的研究兴趣。首先,纳米陶瓷研磨体具有优异的磨削性能。由于其颗粒尺寸非常小,因此具有较高的质量比表面积,有利于增加与被磨削材料的接触面积,从而提高磨削效果。此外,纳米颗粒之间的间距较小,使得研磨体的密度较大,有利于提高磨削效率和磨削速率。此外,纳米陶瓷研磨体还具
陶瓷研磨体在降低粉磨电耗中的应用.docx
陶瓷研磨体在降低粉磨电耗中的应用陶瓷研磨体在降低粉磨电耗中的应用摘要:近年来,随着能源的稀缺性和环境保护要求的逐渐提高,陶瓷材料作为一种新型研磨体在降低粉磨电耗方面得到了广泛关注。本文将从陶瓷研磨体的物理化学性质、应用优势及其对粉磨过程的影响等方面进行综述,并探讨其在降低粉磨电耗中的应用。1.引言粉磨过程是固体物料制备的关键环节之一,它对能源的消耗起着至关重要的作用。传统的研磨介质如钢球等具有电导性,容易对磨机产生较大的电耗。而陶瓷研磨体由于其绝缘性质,在电耗方面具有明显的优势。因此,研究陶瓷研磨体在降低
陶瓷研磨体在Φ4.2 m×13 m球磨机上的应用.docx
陶瓷研磨体在Φ4.2m×13m球磨机上的应用摘要:随着科技水平的不断提高,陶瓷研磨体在各个领域逐渐得到了广泛的应用,特别是在球磨工艺中的应用越来越受到人们的青睐。本文主要探讨了陶瓷研磨体在Φ4.2m×13m球磨机中的应用,分析了其应用效果和优点,对研究陶瓷研磨体的发展趋势进行了一定的展望。关键词:陶瓷研磨体;球磨机;应用效果;发展趋势一、概述球磨工艺作为一种重要的物料研磨粉碎方法,广泛应用于建材、冶金、化工、电力、轻工、矿山等行业,能够实现高效、低成本、能耗低等特点。而陶瓷研磨体作为球磨工艺中不可或缺的重
永祥公司再用陶瓷研磨体技术.docx
永祥公司再用陶瓷研磨体技术永祥公司是一家专业从事陶瓷研磨体技术的公司,其致力于在材料科学和工程领域进行创新,以提供专业化的陶瓷研磨体产品和解决方案,为客户在精细加工和制造领域提供高质量的选项。本文将介绍关于永祥公司的陶瓷研磨体技术的相关背景,重点研究其中的技术及用途。1.背景研磨体是用于研磨、打磨和抛光的小块材料,被广泛应用于机械制造、金属加工、电子材料等行业。目前市场上主要的研磨体材料有陶瓷、玻璃和金刚石等,其中陶瓷研磨体是一种优秀的耐磨材料,具有硬度高、密度大、耐高温等特点,在制造和加工领域得到了广泛