
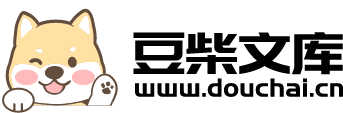
PCB镀层缺陷成因分析及其对策.docx
猫巷****雪凝
在线预览结束,喜欢就下载吧,查找使用更方便
相关资料
PCB镀层缺陷成因分析及其对策.docx
编号:时间:2021年x月x日书山有路勤为径学海无涯苦作舟页码:PCB鍍層缺陷成因分析及其對策[摘要]分析了金属化孔镀层的主要缺陷及产生原因从各主要工序出发提出了如何优化工艺参数进行严格的工艺及生产管理以保证孔化质量的方法。[关键词]多层印制板金属化孔镀层缺陷1前言金属化孔质量与多层板质量及可靠性息息相关。金属化孔起着多层印制线路电气互连的作用。孔壁镀铜层质量是印制板质量的核心不仅要求镀层有合适的厚度、均匀性和延展性而且要求镀层在288℃热冲击10秒不能
PCB镀层缺陷成因分析及其对策.docx
编号:时间:2021年x月x日书山有路勤为径,学海无涯苦作舟页码:第页共NUMPAGES9页第PAGE\*MERGEFORMAT9页共NUMPAGES\*MERGEFORMAT9页PCB鍍層缺陷成因分析及其對策[摘要]分析了金属化孔镀层的主要缺陷及产生原因,从各主要工序出发,提出了如何优化工艺参数,进行严格的工艺及生产管理,以保证孔化质量的方法。[关键词]多层印制板,金属化孔,镀层缺陷1前言金属化孔质量与多层板质量及可靠性息息相关。金属化孔起着多层印制线路电气互连的作用。
PCB镀层缺陷成因分析及其对策.doc
PCB鍍層缺陷成因分析及其對策[摘要]分析了金属化孔镀层的主要缺陷及产生原因从各主要工序出发提出了如何优化工艺参数进行严格的工艺及生产管理以保证孔化质量的方法。[关键词]多层印制板金属化孔镀层缺陷1前言金属化孔质量与多层板质量及可靠性息息相关。金属化孔起着多层印制线路电气互连的作用。孔壁镀铜层质量是印制板质量的核心不仅要求镀层有合适的厚度、均匀性和延展性而且要求镀层在288℃热冲击10秒不能产生断裂。因为孔壁镀铜层热冲击断裂是一种致命的缺陷它将造成内层线路间和内层与外层线路之间断路;轻者影
多层pcb金属化孔镀层缺陷成因分析及对策(二).doc
深圳金百泽电子科技股份有限公司(www.kbsems.com)成立于1997年,是线路板行业十强企业,总部设在深圳,研发和生产分布在深圳、惠州和西安等地,为客户提供产品研发的PCB设计、PCB快速制造、SMT加工、组装与测试及硬件集成等垂直整合解决方案,是国内最具特色的电子制造服务提供商。电话:0755-26546699-223多层PCB金属化孔镀层缺陷成因分析及对策(二)2.2孔壁去树脂沾污及凹蚀处理工序首先应该指出,凹蚀与去沾污是两个互为关联,但又相互独立的概念和工艺过程。所谓凹蚀,是指为了充分暴露多
多层pcb金属化孔镀层缺陷成因分析及对策(三).doc
深圳金百泽电子科技股份有限公司(www.kbsems.com)成立于1997年,是线路板行业十强企业,总部设在深圳,研发和生产分布在深圳、惠州和西安等地,为客户提供产品研发的PCB设计、PCB快速制造、SMT加工、组装与测试及硬件集成等垂直整合解决方案,是国内最具特色的电子制造服务提供商。电话:0755-26546699-223多层PCB金属化孔镀层缺陷成因分析及对策(三)2.3电镀工序2.3.1电镀前的板材处理??化学粗化为了保证化学镀铜层与基体铜箔的结合力,在化学镀铜(沉铜)前,必须对铜箔表面进行一次