
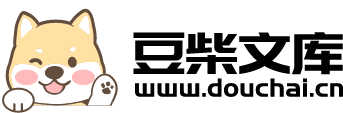
聚合反应器的分类介绍全解.ppt
YY****。。
亲,该文档总共12页,到这已经超出免费预览范围,如果喜欢就直接下载吧~
相关资料
聚合反应器的分类介绍全解.ppt
聚合反应特点:反应机理复杂,聚合方法多样,且大多数反应体系随着聚合反应的进行,体系中的粘度急剧上升,物料粘壁等现象给聚合反应器的选型和设计带来一定的难度。聚合反应器的型式及特点2.管式(塔式)反应器管式(塔式)聚合反应器的构造比较简单,这种反应器一般用于处理粘度较高的均相反应物料。它属于连续流动反应器,原料从管的一端连续送入,在管内完成升温、反应等,而产物和未反应的单体从另一端连续排出。3.特种反应器对处理高粘度的聚合体系,如本体聚合或缩聚反应后期,反应物料的粘度可达500一5000Pa·s,故需采用特殊
聚合反应器的分类介绍ppt课件.ppt
聚合反应特点:反应机理复杂,聚合方法多样,且大多数反应体系随着聚合反应的进行,体系中的粘度急剧上升,物料粘壁等现象给聚合反应器的选型和设计带来一定的难度。聚合反应器的型式及特点2.管式(塔式)反应器管式(塔式)聚合反应器的构造比较简单,这种反应器一般用于处理粘度较高的均相反应物料。它属于连续流动反应器,原料从管的一端连续送入,在管内完成升温、反应等,而产物和未反应的单体从另一端连续排出。3.特种反应器对处理高粘度的聚合体系,如本体聚合或缩聚反应后期,反应物料的粘度可达500一5000Pa·s,故需采用特殊
常用风机分类介绍全解.ppt
常用风机介绍风机的分类离心式风机离心式风机的工作原理离心式风机按其产生风压高低可分为:轴流式风机轴流式风机的工作原理是:旋转叶片的挤压推进力使流体获得能量,升高其压能和动能,其结构如图所示。叶轮1安装在圆锥形3内,当叶轮旋转时,流体轴向流入,在叶片叶道内获得能量后,沿轴向流出。轴流式风机适用于大流量、低压力,制冷系统中常用作送引风机轴流式风机风压一般在450N/平方米~4500N/平方米之间,主要用于矿井、隧道、船舰仓室的通风;纺织厂通风、工业作业场所的通风、降温;化工气体排送;热电厂锅炉的通风、引风;热
压力管道的分类全解.ppt
压力管道分类压力管道分类压力管道分类压力管道分类压力管道分类压力管道分类压力管道分类压力管道分类压力管道分类压力管道分类压力管道分类GC类级别划分示意GC类级别划分示意
文本分类全解.ppt
数据挖掘:文本分类专题主要内容文本分类文本分类新闻的特征向量例如词汇表有64000个词,其编号分别为1,2,...,64000统计一篇新闻中各词的出现次数,按照对应词在词汇表中的位置依次排列,就得到一个向量新闻的特征向量新闻的特征向量词频的简单应用主要内容度量两篇新闻的相似度余弦相似度余弦相似度余弦相似度练习应用:论文分组主要内容分类系统设计的基本步骤应用:新闻分类应用:新闻分类-使用kNN应用:新闻分类-使用朴素贝叶斯主要内容逆文档频率(TF-IDF)逆文档频率(TF-IDF)逆文档频率(TF-IDF)