
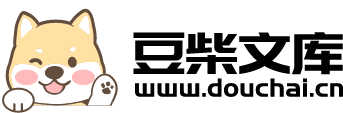
精益生产——换型与防错.ppt
YY****。。
亲,该文档总共109页,到这已经超出免费预览范围,如果喜欢就直接下载吧~
相关资料
精益生产——换型与防错.pptx
精益生产——换型与防错.ppt
市场已经变得越来越无情和浮躁!交期短,品种多,批量小,变化大,同质化,价格下滑,成本上升,品质严格,操作无序,订单易变,客户挑剔,拖欠货款贸易保护,产权纷争等等,都成了阻碍业务进一步发展的堡垒。那么,在这样日趋严峻的形势面前,企业应该怎么办呢?提高管理素质,减少浪费损失;实施差异化管理,开发蓝海战略;整合优势资源,积聚核心价值;培养员工队伍,打造创新能力;然后,在此基础上先把自己做强,再谋图做大,应该是关键。题记精益生产第一部分精益生产原理解析精益生产湖面效应LP的动力精益生产的必由之路1、JIT(JUS
精益生产之快速换型与防错(1).ppt
市场已经变得越来越无情和浮躁!交期短,品种多,批量小,变化大,同质化,价格下滑,成本上升,品质严格,操作无序,订单易变,客户挑剔,拖欠货款贸易保护,产权纷争等等,都成了阻碍业务进一步发展的堡垒。那么,在这样日趋严峻的形势面前,企业应该怎么办呢?提高管理素质,减少浪费损失;实施差异化管理,开发蓝海战略;整合优势资源,积聚核心价值;培养员工队伍,打造创新能力;然后,在此基础上先把自己做强,再谋图做大,应该是关键。题记精益生产课程内容提要第一部分精益生产原理解析精益生产启示湖面效应LP的动力转变观念与生产方式生
精益生产之快速换型与防错(1).pptx
市场已经变得越来越无情和浮躁!交期短,品种多,批量小,变化大,同质化,价格下滑,成本上升,品质严格,操作无序,订单易变,客户挑剔,拖欠货款贸易保护,产权纷争等等,都成了阻碍业务进一步发展的堡垒。那么,在这样日趋严峻的形势面前,企业应该怎么办呢?提高管理素质,减少浪费损失;实施差异化管理,开发蓝海战略;整合优势资源,积聚核心价值;培养员工队伍,打造创新能力;然后,在此基础上先把自己做强,再谋图做大,应该是关键。题记精益生产第一部分精益生产原理解析精益生产湖面效应LP的动力精益生产的必由之路1、JIT(JUS
精益生产之快速换型与防错(1).ppt
市场已经变得越来越无情和浮躁!交期短品种多批量小变化大同质化价格下滑成本上升品质严格操作无序订单易变客户挑剔拖欠货款贸易保护产权纷争等等都成了阻碍业务进一步发展的堡垒。那么在这样日趋严峻的形势面前企业应该怎么办呢?提高管理素质减少浪费损失;实施差异化管理开发蓝海战略;整合优势资源积聚核心价值;培养员工队伍打造创新能力;然后在此基础上先把自己做强再谋图做大应该是关键。题记精益生产课程内容提要第一部分精益生产原理解析精益生产启示湖面效应LP的动力转变观念与生产方式生产运作系统精益生产的必由之