
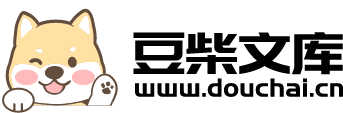
案例分析_重大安全事故.pdf
努力****亚捷
亲,该文档总共117页,到这已经超出免费预览范围,如果喜欢就直接下载吧~
相关资料
案例分析_重大安全事故.pdf
重大安全事故案例分析主要内容:案例一、博帕尔化学品泄漏事故案例二、BP德克萨斯炼油厂爆炸事故案例三、吉化“11.13”特大爆炸事故案例四、重庆市开县气矿井喷事故案例五、美国羟胺蒸馏装置爆炸事故案例六、长滩天然气工厂爆炸事故案例七、休斯顿化工区爆炸事故案例八、Piper舢曲既海上平台沉没事故案例九、英国邦斯菲尔德油库爆炸火灾事故案例十、重庆天原化工“4.16”氯气泄漏爆炸事故案例一、博帕尔化学品泄漏事故1984年12月3日发生在印度博帕尔的甲基异氰酸酯(methylisocyanate简称MIC)泄
案例分析_重大安全事故.pdf
重大安全事故案例分析主要内容:案例一、博帕尔化学品泄漏事故案例二、BP德克萨斯炼油厂爆炸事故案例三、吉化“11.13”特大爆炸事故案例四、重庆市开县气矿井喷事故案例五、美国羟胺蒸馏装置爆炸事故案例六、长滩天然气工厂爆炸事故案例七、休斯顿化工区爆炸事故案例八、Piper舢曲既海上平台沉没事故案例九、英国邦斯菲尔德油库爆炸火灾事故案例十、重庆天原化工“4.16”氯气泄漏爆炸事故案例一、博帕尔化学品泄漏事故1984年12月3日发生在印度博帕尔的甲基异氰酸酯(methylisocyanate,简称MIC)泄漏事故
北京清华附中重大安全事故案例分析.ppt
清华大学附属中学体育馆及宿舍楼工程(以下简称“清华附中工程”)位于中关村北大街清华大学附属中学校园内总建筑面积20660平方米是集体育、住宿、餐厅、车库为一体的综合楼。该建筑地上五层、地下两层。地上分体育馆和宿舍楼两栋单体地下为车库及人防区。事发部位位于基坑3标段深约13米、宽约42.2米、长约58.3米。现场情况如下:已经完成3标段下层钢筋的绑扎、马凳安放、上层钢筋的铺设等工作马凳采用直径25mm或28mm的带肋钢筋焊制(方案要求32mm)安放间距为0.9至2.1米(方
北京清华附中重大安全事故案例分析.ppt
清华大学附属中学体育馆及宿舍楼工程(以下简称“清华附中工程”)位于中关村北大街清华大学附属中学校园内,总建筑面积20660平方米,是集体育、住宿、餐厅、车库为一体的综合楼。该建筑地上五层、地下两层。地上分体育馆和宿舍楼两栋单体,地下为车库及人防区。事发部位位于基坑3标段,深约13米、宽约42.2米、长约58.3米。现场情况如下:已经完成3标段下层钢筋的绑扎、马凳安放、上层钢筋的铺设等工作马凳采用直径25mm或28mm的带肋钢筋焊制(方案要求32mm),安放间距为0.9至2.1米(方案要求1米);马凳横梁与
北京清华附中重大安全事故案例分析.ppt
清华大学附属中学体育馆及宿舍楼工程(以下简称“清华附中工程”)位于中关村北大街清华大学附属中学校园内,总建筑面积20660平方米,是集体育、住宿、餐厅、车库为一体的综合楼。该建筑地上五层、地下两层。地上分体育馆和宿舍楼两栋单体,地下为车库及人防区。事发部位位于基坑3标段,深约13米、宽约42.2米、长约58.3米。现场情况如下:已经完成3标段下层钢筋的绑扎、马凳安放、上层钢筋的铺设等工作马凳采用直径25mm或28mm的带肋钢筋焊制(方案要求32mm),安放间距为0.9至2.1米(方案要求1米);马凳横梁与