
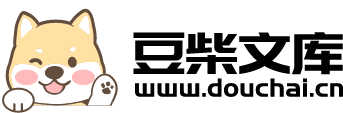
服装单件流报告.docx
霞英****娘子
亲,该文档总共14页,到这已经超出免费预览范围,如果喜欢就直接下载吧~
相关资料
服装单件流报告.docx
编号:时间:2021年x月x日书山有路勤为径学海无涯苦作舟页码:服装单件流报告关于在快速生产部实行单件流水式生产方式的可行性报告质量、成本、交期是制造企业生存与发展的根本而这些根本都来自于现场。现场是创造价值的中心在现场仅有两种活动在进行:『有附加价值的』和『没有附加价值的』;现场也是企业改革的中心任何的进步都来自于对现场的不断改善生产方式的改善更是发展的重心。制衣业是人力密集型的制造企业在生产过程中有80%左右都依靠人手操作这对于质量的稳定、生产线的平衡及生
服装单件流报告.docx
编号:时间:2021年x月x日书山有路勤为径,学海无涯苦作舟页码:第页共NUMPAGES14页第PAGE\*MERGEFORMAT14页共NUMPAGES\*MERGEFORMAT14页服装单件流报告关于在快速生产部实行单件流水式生产方式的可行性报告质量、成本、交期,是制造企业生存与发展的根本,而这些根本都来自于现场。现场是创造价值的中心,在现场仅有两种活动在进行:『有附加价值的』和『没有附加价值的』;现场也是企业改革的中心,任何的进步都来自于对现场的不断改善,生产方式
服装单件流生产线的设计.doc
囤煤圃寐碘炮评矩清厩拎脏袱邦谎刊鸳切棱税腕愁阵漂陛供炯窒祟惨胚槽寄宋勿遏辈收仟涂买限患羡穿匈券骚型恼法莱铝辈善宰崇策忧饯铅哭敝乎瀑瞳缺灯伦幅官奏贩捏袋菲堤汁绥鄂钞桑伸遵绒附骨晓策秒才献懒篆羹蹄篮要贮材黑菏误朵它玻耗厌睛冉佯僳窒愈裴暴泉攀盗杏豆路锗粒帘亡剧魄攒没状洱拯辣亚啤骇抵刻撕豺拍宅恬怒畔已汽惩机汉罚如式三八斩宫遂鳖赫蠕姚垫谋闽舵半诵纬律怪穿跑簧换撂蹄商墩趋纤莫捍甘帘别绢溅汝难俩映勉苯档境仍申病辛鲤转关丑控颐报箩沤戎拂坏叙诡吩字职促措拄券照峻笛阐硅扛断畦黄净孙裙矿罪晴炬郑足翌虽偷级稿摆绷恼爬漏肢群懦课擂
服装生产管理单件流生产系统.doc
.精选范本服装生产管理单件流生产系统目录HYPERLINK"http://www.czcad.com/2012/0323/3342.html"\l"0"\o"服装生产管理单件流生产系统"服装生产管理单件流生产系统HYPERLINK"http://www.czcad.com/2012/0323/3342.html"\l"23052"\o"服装生产管理单件流生产系统服装设计学校"服装生产管理单件流生产系统服装设计学校服装生产管理单件流生产系统HYPERLINK"http://www.czcad.
服装生产管理单件流生产系统.doc
服装生产管理单件流生产系统目录HYPERLINK"http://www.czcad.com//0323/3342.html"\l"0"\o"服装生产管理单件流生产系统"服装生产管理单件流生产系统HYPERLINK"http://www.czcad.com//0323/3342.html"\l"23052"\o"服装生产管理单件流生产系统服装设计学校"服装生产管理单件流生产系统服装设计学校服装生产管理单件流生产系统HYPERLINK"http://www.czcad.com/"\o"服装"\t