
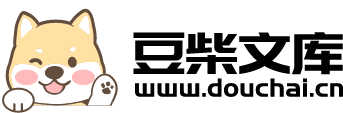
基于数值模拟的导叶铸造缺陷分析及工艺优化.docx
快乐****蜜蜂
在线预览结束,喜欢就下载吧,查找使用更方便
相关资料
基于数值模拟的导叶铸造缺陷分析及工艺优化.docx
基于数值模拟的导叶铸造缺陷分析及工艺优化引言导叶作为涡轮机器的重要部件,需要具有良好的流动特性和压力差能力。而其制造过程中出现的各种缺陷会严重影响导叶的性能和寿命。因此,研究导叶铸造缺陷的成因和解决方案,具有很高的实际应用价值。本文主要针对导叶铸造过程中出现的缺陷进行分析和优化。首先,利用数值模拟技术对导叶铸造过程中可能出现的缺陷进行建模和模拟。然后,根据模拟结果,采取相应的工艺措施进行优化。最后,对优化后的制造工艺进行实验验证,以进一步确定优化效果。一、导叶铸造缺陷成因1.1短流缺陷短流缺陷是指在导叶铸
基于MAGMAsoft数值模拟的水轮机导叶铸造工艺研究.docx
基于MAGMAsoft数值模拟的水轮机导叶铸造工艺研究引言水轮机导叶作为水轮机的重要组成部分,其质量直接影响水轮机的性能和寿命。为保证水轮机导叶的质量,需要优化其铸造工艺。本文基于MAGMAsoft数值模拟,对水轮机导叶的铸造工艺进行了研究。一、水轮机导叶的结构与材料选择水轮机导叶结构较为复杂,一般由导叶体和尾板组成。导叶体一般采用铜合金材料,尾板则选用碳素钢或不锈钢。导叶体的铸造工艺对其性能影响较大,因此需要对其铸造工艺进行深入研究。二、铸造工艺分析铸造工艺对铸件质量的影响十分重要,因此需要进行工艺分析
铸造缺陷分析及工艺优化措施.docx
铸造缺陷分析及工艺优化措施铸造是一种重要的制造方法,其中铸造缺陷是不可避免的,这些缺陷可能会导致工件的性能下降,也会增加生产成本。因此,对铸造缺陷进行分析并采取相应的工艺优化措施是非常重要的。铸造缺陷的分类1.表面缺陷:表面缺陷是在工件表面产生的缺陷,例如气孔、夹渣和氧化皮等。2.内部缺陷:内部缺陷是在工件内部产生的缺陷,例如疏松、气泡和裂缝等。3.构造缺陷:构造缺陷是由于材料中的不同构造或纹理而产生的缺陷,例如异种析出和夹杂等。铸造缺陷的成因1.金属流动不畅:金属流动不畅会导致气孔、冷隆和缩孔等表面和内
基于数值模拟的大型发电飞轮铸造工艺优化.docx
基于数值模拟的大型发电飞轮铸造工艺优化摘要本论文以大型发电飞轮铸造工艺优化为研究对象,通过数值模拟的方法进行建模,并通过参数优化和试验考察等方法对其进行分析和优化,以提高生产效率和降低生产成本。研究结果表明:处理温度、压力、组合模塑速等参数对铸造质量和生产成本有较大影响,通过优化这些参数可以大幅提高铸造的质量和效率。关键词:大型发电飞轮、铸造、工艺优化、数值模拟。AbstractThisthesisfocusesontheoptimizationofthecastingprocessoflarge-sca
基于ViewCast的顶盖砂型铸造工艺数值模拟及优化.docx
基于ViewCast的顶盖砂型铸造工艺数值模拟及优化摘要本文基于ViewCast软件,对顶盖砂型铸造工艺进行数值模拟及优化研究。通过建立顶盖砂型铸造的三维有限元模型,对铸造过程中的流动、固化和收缩过程进行了数值模拟。通过仿真结果,优化工艺参数,对铸件质量进行了提高和保证。同时,通过优化浇注系统和砂型设计,减少了铸造缺陷,提高了铸件的成形质量。关键词:ViewCast,顶盖砂型铸造,数值模拟,工艺优化,铸造缺陷AbstractInthispaper,basedonViewCastsoftware,numer