
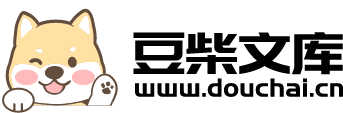
基于Dynaform的多次拉深工序优化设计.docx
快乐****蜜蜂
在线预览结束,喜欢就下载吧,查找使用更方便
相关资料
基于Dynaform的多次拉深工序优化设计.docx
基于Dynaform的多次拉深工序优化设计随着制造业的发展,高质量、高效率的生产成为了制造企业的追求目标。而在生产中,优化生产工序是提高生产效率和质量的关键环节之一。本文以Dynaform为基础,探讨如何对多次拉深工序进行优化设计。多次拉深指的是成型中需要多次拉深来达到所需形状的工序。多次拉深方式有很多种,比如:单次深拉、多次浅拉、等压拉深等等。在实际生产中,多次拉深工序经常出现形状不对、收缩率过大、边角处出现断裂等问题。这些问题一方面会增加生产成本,另一方面也会影响产品的质量。在实际操作中,可以通过以下
基于Dynaform软件和正交试验相结合的拉深工艺参数优化.docx
基于Dynaform软件和正交试验相结合的拉深工艺参数优化近年来,随着航空航天、汽车制造等高科技产业的快速发展,拉深加工工艺越来越受到重视。为了提高拉深工艺的质量和效率,优化拉深加工工艺参数成为了研究的热点之一。本文通过Dynaform软件和正交试验相结合的方法,对拉深工艺进行参数优化研究。首先,介绍了拉深加工的定义、特点以及优化参数的意义。拉深加工是一种板材成形技术,是将平面板片拉伸成各种形状的过程。它的特点是能够减少板材的厚度,提高材料的利用率,并且能够使产品的形状更加多样化。而优化拉深加工工艺参数则
基于Dynaform的汽车覆盖件拉深成形分析.docx
基于Dynaform的汽车覆盖件拉深成形分析引言汽车覆盖件的生产是汽车制造领域的重要组成部分,其生产过程包括数控加工、锻造、拉深成形等。而拉深成形是一种重要的变形加工方法,其具有成形快速、工艺简单、加工范围广等特点,在汽车制造过程中得到广泛应用。本文主要介绍基于Dynaform的汽车覆盖件拉深成形分析。1.Dynaform简介Dynaform是一款基于有限元分析(FEA)技术的CAD软件,它可以用于汽车覆盖件的成形模拟。Dynaform具有灵活的参数设置和模拟功能,可以帮助工程师快速的预测并分析汽车覆盖件
基于DYNAFORM的铝箔拉深成形数值模拟研究.docx
基于DYNAFORM的铝箔拉深成形数值模拟研究基于DYNAFORM的铝箔拉深成形数值模拟研究摘要随着现代工业的发展,对于高质量、高效率、低成本的产业需求越来越迫切。成形技术作为制造业的重要技术之一,在现代工业中发挥着重要的作用。铝箔作为一种重要的工程材料,在汽车、航空航天等领域得到广泛应用。本文基于DYNAFORM软件,针对铝箔拉深成形过程进行数值模拟研究,旨在改善铝箔成形的质量和效率。关键词:DYNAFORM,铝箔,拉深成形,数值模拟1.引言铝箔作为一种轻质、高强度、耐腐蚀的材料,被广泛应用于汽车制造、
基于Dynaform对拉延筋在板材拉深中的应用研究.docx
基于Dynaform对拉延筋在板材拉深中的应用研究引言板材拉深是金属加工中常见的一种工艺,对于金属的延展性有着较高的要求,而拉延杆正是这种要求的答案。然而,在板材拉深中,拉延杆的应用不仅仅是为了扩大金属的延展性,还需要具备一种良好的延展特性,以便完成设计要求。Dynaform是一款专门用来进行CAE分析的软件,具有丰富的应用场景。本文主要是围绕Dynaform,探讨拉延杆在板材拉深过程中的应用研究。材料与方法基于Dynaform对拉延杆在板材拉深中的应用研究,主要包括以下步骤:1.建立模型2.定义材料属性