
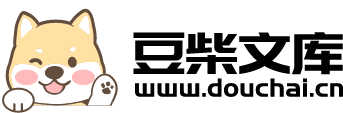
环氧官能化弹性体增韧PET的研究.docx
快乐****蜜蜂
在线预览结束,喜欢就下载吧,查找使用更方便
相关资料
环氧官能化弹性体增韧PET的研究.docx
环氧官能化弹性体增韧PET的研究环氧官能化弹性体增韧聚对苯二甲酸乙二醇酯(PET)的研究摘要:聚对苯二甲酸乙二醇酯(PET)是一种广泛应用于各个领域的工程塑料。然而,纯PET材料的韧性较差,常常导致脆性断裂。本文研究了环氧官能化弹性体对PET进行增韧的方法和效果。通过将环氧官能化弹性体添加到PET中,形成共混体系,并对其力学性能、热性能和断裂行为进行了研究。结果表明,环氧官能化弹性体的添加显著改善了PET的韧性,使其具有更好的拉伸和冲击性能。此外,环氧官能化弹性体的添加还提高了PET的热稳定性和断裂韧性。
HDPE的官能化及对废PET增韧的研究.docx
HDPE的官能化及对废PET增韧的研究摘要:高密度聚乙烯(HDPE)是一种广泛应用于工业和生活领域的重要塑料,具有优异的物理和化学性质。本文主要介绍了几种常见的HDPE官能化方法及其对废PET增韧效果的研究。结果表明,HDPE与不同类型的功能化剂反应可以大大改善HDPE的力学性能和热稳定性。此外,HDPE也可以作为一种优秀的增韧剂添加到废PET中,以提高废PET的力学性能和阻燃性能。关键词:高密度聚乙烯、官能化、废PET、增韧引言:高密度聚乙烯(HDPE)是一种广泛应用于工业和生活领域,具有许多优异的性能
环氧官能化ABS增韧PBT树脂的性能研究.docx
环氧官能化ABS增韧PBT树脂的性能研究标题:环氧官能化ABS增韧PBT树脂的性能研究摘要:本研究旨在通过环氧官能化ABS来增韧聚对苯二甲酸丁二酯(PBT)树脂,探索其性能改善效果。通过添加不同比例的环氧树脂到ABS中,然后与PBT进行共混,制备出增韧PBT复合材料,并对其力学性能、热性能和热稳定性进行测试。研究结果显示,环氧官能化ABS能够有效提高增韧PBT树脂的力学性能和热性能,且具有较好的热稳定性,为优化ABS/PBT复合材料的应用提供一定的理论基础。1.引言ABS和PBT作为两种常见的工程塑料,具
PPR的官能化及其对回收PET瓶片的增韧研究.docx
PPR的官能化及其对回收PET瓶片的增韧研究摘要本文主要探讨了聚丙烯的官能化及其增韧回收PET瓶片的应用。首先介绍了聚丙烯的结构和性质,其次阐述了聚丙烯的官能化方法,并详细介绍了增韧剂的种类和作用机理。最后,对回收PET瓶片的应用进行了深入探讨,分析了回收PET瓶片的优缺点以及聚丙烯增韧回收PET瓶片的应用前景。本文旨在为聚丙烯官能化和PET瓶片回收利用的研究提供参考。关键词:聚丙烯,官能化,回收PET瓶片,增韧剂,应用前景引言聚丙烯(PP)是一种重要的工程塑料,其物理化学性质稳定,机械强度高,热稳定性好
增韧环氧胶和弹性环氧胶的研究.docx
增韧环氧胶和弹性环氧胶的研究一、引言环氧胶作为一种广泛应用于工业领域的粘接材料,由于其具有优良的物理和化学性能而备受青睐。然而,环氧胶在某些情况下还存在一些缺陷,常常会出现断裂、开裂和脆化等问题,这对工业生产和产品的使用造成了一定的影响。因此,研究和开发增韧环氧胶和弹性环氧胶已成为当前环氧胶研究的热点之一。二、增韧环氧胶的研究进展增韧环氧胶是一种增加环氧胶抗拉、弯曲、抗剪强度和韧性的新型胶黏剂。其主要的研究方向在于材料的选择和制备方法的改进。一些研究表明,将碳纤维、纳米颗粒、橡胶、树脂等添加到环氧胶中可以