
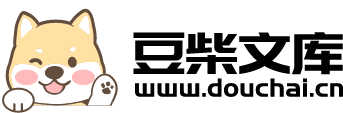
基于三坐标测量机的螺旋锥齿轮加工参数反调修正.docx
快乐****蜜蜂
在线预览结束,喜欢就下载吧,查找使用更方便
相关资料
基于三坐标测量机的螺旋锥齿轮加工参数反调修正.docx
基于三坐标测量机的螺旋锥齿轮加工参数反调修正摘要螺旋锥齿轮是一种常用的传动元件,其加工精度对于传动系统的性能有着重要的影响。在加工过程中,由于加工误差和机床误差等因素的影响,会导致加工后的实际齿形与设计要求不符。本文借助三坐标测量机,对螺旋锥齿轮加工过程中的参数进行了反调修正。通过设计实验,得出了加工参数对于齿形误差的影响规律,进而调整加工参数,使得加工后的齿形误差能够被有效减小。实验结果表明,本文所提出的反调修正方法能够有效提高螺旋锥齿轮加工的精度和质量。关键词:螺旋锥齿轮;加工参数;三坐标测量机;反调
螺旋锥齿轮形性协同加工参数混合反调修正方法.pdf
本发明公开了一种螺旋锥齿轮形性协同加工参数混合反调修正方法,给出一种几何与物理性能协同优化方案,优化目标是可任意预设的ease‑off齿面,优化结果是带反调量的精确加工参数,使反调过程变成理论设计齿面向预设ease‑off目标齿面的无穷最小化逼近过程,逼近程度定义残余ease‑off来评判。考虑ease‑off齿面的高阶性能,建立考虑误差齿面高阶特性的可预设制造精度的通用加工参数反调模型,优化加工参数为最优设计变量,考虑建立目标函数的强烈非线性,并探究其原因,提供更高效更精确更稳定的非线性最小二乘鲁棒性算
可预设精度的螺旋锥齿轮加工参数反调修正计算方法.pdf
本发明提供了一种可预设精度的螺旋锥齿轮加工参数反调修正计算方法,在基本齿面和设计齿面之间预设一个考虑误差范围的过度齿面作为目标齿面,以目标齿面作为设计齿面的逼近齿面,逼近程度以残余ease‑off作为评价标准。整个反调过程变成理论设计齿面先预设ease‑off目标齿面的无穷最小化逼近过程,逼近程度则定义残余ease‑off来评判,使得求解的精确参数具有灵活性和实用性,且保证了求解的参数具有足够的精度。建立了考虑误差齿面高阶特性的可预设制造精度的通用加工参数反调模型,充分探究造成目标函数强烈非线性的原因,通
螺旋锥齿轮形性协同制造参数驱动混合反调及控制方法.pdf
本发明公开了一种螺旋锥齿轮形性协同制造参数驱动混合反调及控制方法,优化目标是可任意预设的ease‑off齿面,优化结果是带反调量的精确加工参数。使反调过程变成理论设计齿面向预设ease‑off目标齿面的无穷最小化逼近过程,逼近程度定义残余ease‑off评判。考虑ease‑off齿面的高阶性能,建立考虑误差齿面高阶特性的可预设制造精度的通用加工参数反调模型,优化加工参数为最优设计变量,考虑建立目标函数的强烈非线性并探究其原因,提供更高效更精确更稳定的含双Dogleg步的信赖域算法。同时借助LTCA的主要手
弧齿锥齿轮基于比例修正参数的齿形误差修正.docx
弧齿锥齿轮基于比例修正参数的齿形误差修正摘要:弧齿锥齿轮是机械传动中常用的一种重要的元件。在加工制造过程中,由于切削加工等原因,会产生一定的齿形误差,这会对齿轮的传动效率、噪声等性能造成一定的影响。因此需要对其进行齿形误差修正。本文分析了弧齿锥齿轮的齿形误差产生原因,探讨了基于比例修正参数的齿形误差修正方法,数值仿真结果表明该方法有效降低了齿形误差,提高了齿轮的传动效率和工作稳定性。关键词:弧齿锥齿轮;齿形误差;比例修正参数;传动效率;工作稳定性引言:弧齿锥齿轮是机械传动中常用的一种元件。它具有结构简单、